With the rollout of 5G and 6G discussions already beginning, it’s no surprise that the only known for new telecommunication standards will be higher frequencies, well into the mmWave frequencies beyond 100 GHz. Whether in the RF or optical domains, R&D development is ongoing, raising the question: how will engineers address broadband and mmWave measurements moving forward? In parallel with the many interesting 110 GHz and higher use cases, the idea of modernizing measurements from the instrument to the device under test is a relevant topic of conversation. To enable new test systems to address these changing frequency requirements, we must migrate from the nearly 100-year-old waveguide to newer coaxial solutions. While the idea of modernizing measurements has its roots in reducing the complexity of test setups, frequency and time domain measurements will benefit by moving to coaxial solutions for mmWave measurements.
This article explores the drivers for mmWave application development, discusses technologies for performing measurements to 110 GHz, identifies the trade-offs between waveguide and coaxial technology and acknowledges the new coaxial solutions coming on the market.
EMERGING MARKETS
We’re seeing significant development in the telecommunications sector fueling the need for mmWave frequency coverage. Denser networks using microwave backhaul, fronthaul and fixed wireless are predicted to exceed 100 GHz to support the deployment of 5G and development of 6G and beyond.1 These frequency requirements come from new antennas and transceivers to provide more accessibility and data to users, as well as the optoelectrical components needed to move tremendous amounts of data from the radio through the network, parallel developments to provide 800G or 1.6T Ethernet capabilities.
Another market active for some time is automotive radar. Short- and long-range automotive radar uses the 76 to 81 GHz band and, like all radar, includes a transceiver that requires testing of internal components like amplifiers, mixers and antennas. While the radar frequencies fall within the band addressed by the new 1.35 mm connector, which spans DC to 90 GHz, there is no component support currently, other than adapters. The new applications are not limited to the consumer: electronic warfare and satellite transmission use W-Band frequencies. As semiconductor process technologies improve, device characterization requires measurement coverage from near DC to 110 GHz.
WHERE DO MEASUREMENTS FIT?
While these new applications are at the forefront of technology, the supporting measurements often rely on older technology.
Before discussing improving the measurements for these applications, consider the test equipment used for these measurements. For example, before a power sensor can be used in the field, it undergoes various manufacturing tests and calibration - such as a leveling loop calibration, which uses a reference sensor as the correlation standard for the power sensor as both measure a test signal.2 For broadband characterization, from kHz/MHz to the 110 GHz range, it would take many components and adapters to perform this testing without using a broadband coaxial component. And there are other measurements and functionality tests required in production to assure the test instrument is ready to use. All would also benefit from using coaxial components to simplify testing and improve measurement accuracy.
In addition to the test equipment, the components used for various measurements include:
- Intermodulation distortion (IMD) and related measurements that require equal signal distribution using a power divider
- Antenna and active device biasing through a bias tee or Kelvin bias tee
- Spurious signal sampling or optical modulator mismatch correction using a directional coupler
- Receiver compression avoidance or test port VSWR improvement with attenuators
- Gain, compression and isolation using a power splitter
These are not exhaustive, just a few of the many measurements needed to quantify performance and harder to make at mmWave frequencies, where the components may be scarce or unavailable.
MEASUREMENT CHALLENGES
Can you imagine a future where only books are used for information, even though we have the internet? Or driving only gasoline-powered automobiles when electric and hybrid models are available? Of course not. When options exist, the use case dictates which one we use. The same is true of measurements, particularly the choice of components, as technology moves forward.
Waveguide was developed in the 1930s and used widely during World War II. Waveguide components continue to be the de facto standard for high-power signals and frequencies above 70 GHz. Unlike coaxial components, waveguide has nearly zero signal loss, as it is not resistive. This is important because the signal is conserved. Unfortunately, waveguide only operates in specific frequency bands, which precludes broadband measurement.
For frequencies higher than 70 GHz, there are few choices for components other than waveguide. To provide alternatives, the industry is developing new coaxial components, such as the V connector (1.85 mm), However, the V connector has a theoretical limit of 73.3 GHz; the performance above the theoretical limit suffers from over-moding. Over-moding refers to a notable resonance that manifests as an attenuation spike over a small bandwidth. It occurs where the input signal energy changes modes due to impedance and velocity mismatches at the dielectric support bead and air dielectric interface - which is not desirable. This is one of the rare times where a coaxial structure behaves like a waveguide, i.e., not in a single mode.

Figure 1 Typical 110 GHz cable loss vs. frequency.
Users desiring to stay in a native coaxial environment often create makeshift components. One example is using a DC to 110 GHz cable to create an attenuator with broad frequency coverage. A 10 cm long cable provides 3 dB of attenuation at the upper frequency, around 100 GHz (see Figure 1). To create an attenuator with 10 dB loss, three cables could be used, requiring multiple interconnects between the cables and creating measurement uncertainty. A good attenuator is generally flat, i.e., within 1 dB of the desired level across its frequency band. The flatness of a series of cables cannot be guaranteed, however. With three cables, a large attenuation swing will occur, much higher and lower than 10 dB at various frequencies. Not only will the measurement certainty be degraded by multiple interconnects and varying attenuation, the power delivery versus frequencies will vary due to the frequency slope of the cables. This is not an ideal measurement setup. This highlights how users try alternatives to construct useful coaxial components.
Even using waveguide components is a compromise. Consider active device testing. A waveguide cannot conduct a DC voltage or current; it is an inherent DC block and cannot bias anything. For characterizing active devices, the bias can be added through a test port via a probe during development. However, when the device is part of an assembly in a test jig, a waveguide cannot pass both RF and DC power.
Time domain analysis is a common tool used for device characterization. While we focus on frequency domain measurements, emerging applications will also use the time domain, as it can provide insight into impedance characteristics and discontinuities (lowpass time domain), faulty areas in the setup (bandpass time domain) and the electrical quality of a signal through a device or component (an eye diagram).
Many components used in high speed communications are characterized with both time and frequency plots. Return loss and insertion loss are equally important with the eye diagram and impedance profile. For lowpass time domain and eye diagram processing, low frequency and broad frequency coverage are important. The low frequency component is used for extrapolating the DC term and the broad frequency coverage for resolution of the trace to find any issues. Since a waveguide is band limited, a high frequency waveguide such as W-Band will not have a low frequency component, nor can it provide broad frequency coverage.
TRADE-OFFS
Although waveguide is nearly 100 years old, it still serves a purpose, providing some properties that coaxial solutions cannot. Comparing these two technologies shows the trade-offs between them, trade-offs which can be summarized by physical and electrical parameters (see Table 1).
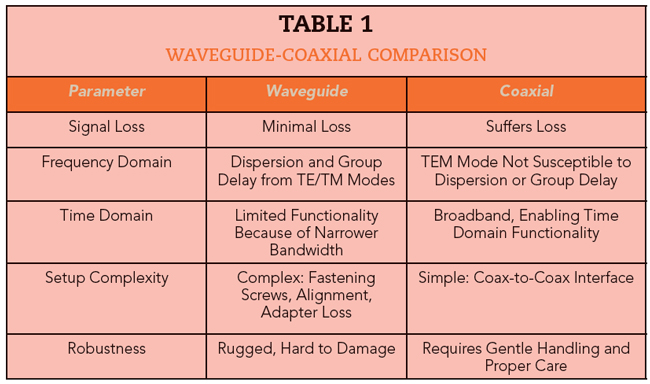
Physical
Waveguide is made from solid metal, and this design quality enables it to be very rugged. Waveguide is not easily damaged and can be dropped without much worry of electrical performance changes, assuming the flange interface is not bent. In comparison, coaxial components with a W connector (1.00 mm) require gentle handling and proper care when using them.
Waveguide has repeatability issues, even with many mechanical mechanisms in place to prevent them. Common knowledge for waveguide users, different users can get different results with the exact same setup. A user can spend a significant amount of time aligning apertures, fastening and torqueing screws and taking other steps to get the best performance from the waveguide component. A coaxial-to-coaxial setup - connecting the test instrument directly to the component - minimizes setup time and ensures repeatability.
Electrical
An advantage of waveguide over coaxial components is transferring higher power across a nearly lossless interface. Coaxial components have lower limits for power transfer, and their structures are resistive, which leads to signal loss. With many setups used for mmWave measurements, an adapter is used to connect between coaxial and waveguide components, and the loss of the coaxial interface reduces some of the advantage of the nearly lossless waveguide. Many applications operate at low power, which is compatible with either waveguide or coaxial components.
Because they are broadband, coaxial components enable more time domain analysis options and support active measurements that require DC bias. The propagation in coaxial components is transverse electromagnetic (TEM), so they do not suffer the effects of dispersion.3 Dispersion affects group delay and impedance, which are concerns using waveguide, as the propagation is either transverse electric or transverse magnetic.
EXTENDED REACH

Figure 2 Anritsu 110 GHz components.
Over the last year, we’ve seen new 110 GHz coaxial components introduced for the mmWave market, including bias tees, DC blocks and directional couplers. Supporting this push to higher frequencies, Anritsu has also introduced various coaxial components including fixed attenuators, a three resistor power divider, a two resistor power splitter, directional coupler, standard and Kelvin bias tees and a broadband DC block (see Figure 2). Anritsu’s components are metrology-grade, with excellent electrical and environmental performance, designed to be used with any measurement equipment that provides coverage to 110 GHz. Such an array of components makes modernizing a test setup straightforward and capable of supporting these new mmWave applications.
References
- D. Gentina, Vision And Future Use of High Millimetre-Wave Bands, 2017.
- R. Collier and A. Skinner, Microwave Measurements, London: Institution of Engineering and Technology, Third Edition, 2007, p. 148.
- R. Collier and A. Skinner, Microwave Measurements. London: Institution of Engineering and Technology, Third Edition, 2007, p. 339.