
Performance, cost and size are key to mobile phone design. Improved performance, lower cost and ever-shrinking module size parameters are universal challenges in the competitive world of mobile phone manufacturing. Over the past four years steady improvements have been made in power amplifier efficiency. Prices have likewise dropped. Yet of the three key standards designers judge new products against, size has seen the most dramatic reduction. While more features are packed into succeeding phone generations, the overall size of the physical handset has remained relatively constant. These added features have created an environment that puts a premium on module and component size.

Over the past four years, GSM power amplifier market suppliers have transitioned from 10 × 10 mm to 7 × 10 mm. The downward trend continued to 7 × 7 mm, 6 × 6 mm and now to 5 × 5 mm (see Figure 1). This trend represents a 30 percent decrease with each new generation and a 50 percent decrease every two years. TriQuint has leapfrogged competitors by going directly from 7 × 7 mm to the 5 × 5 mm generation while maintaining competitive cost and performance.

Fig. 1 The downward trend of power amplifier module size.
The company’s market strategy is intrinsically linked to the goal of developing technologies that support reduced power amplifier module (PAM) size, enhanced performance and reduced cost. These goals were achieved by incorporating three major technologies: flip-chip die and assembly, four-layer substrates, and modules utilizing a single matching die.
Employing flip-chip die has the advantage of locating all I/Os directly below the die. There is no need in flip-chip designs for an additional 0.5 mm beyond the die area typically found in epoxied wirebond designs. Accommodating bond fingers and epoxy run-out disappears from the equation in a flip-chip universe.
The substrate used in module design is also critical. Four-layer substrates provide more flexibility in the area that is dedicated to the output match, and allows for a more compact design.
Finally, the number of discrete surface-mount devices (SMD) present in the module is also critical in reducing overall size. The one passive die in the TQM7M4006 device is approximately the size of two, 02-01 capacitors (including proximity rules) while actually containing seven capacitors for matching, RF blocking and bypassing purposes. These three technologies have led to a more highly effective use of physical area and the ability to build a 5 × 5 mm PAM.
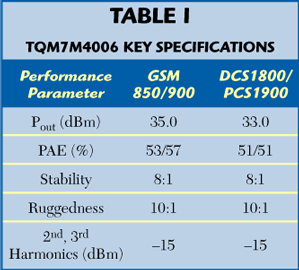
Size and Performance Advantage
Within the TQM7M4006 is a CMOS power control die, two InGaP GaAs (GSM 850/900 and DCS 1800/PCS 1900) PA die, a GaAs passive output matching die and two surface-mount devices (see Figure 2). A low total height of 1.1 mm was obtained by reducing the die thickness to 500 mm. This allows for a 700 mm mold cap to be used on top of the 400 mm substrate. (Table 1 indicates key specifications for the TQM7M4006.)

Fig. 2 The TQM7M4006 PA module.
The TQM7M4006 achieves PAEs of 53 percent (850 MHz), 57 percent (900 MHz) and 51 percent (1800 MHz/1900 MHz), while delivering output power of +35 dBm (low band) and +33 dBm (high band). Undesired coupling was minimized by a thorough module layout. This allows the PAM to achieve stability at load mismatches of 8:1 with –20 dBm of GSM to DCS/PCS crosstalk. The module supports 50 percent duty cycle, or four-slot operation. Figures 3 and 4 show the measured Pout, PAE, and second- and third-harmonic performance of the device.

Fig. 3 GSM 850/900 (a) and DCS 1800/PCS 1900 (b) power output and PAE performance.

Fig. 4 GSM 850/900 (a) and DCS 1800/PCS 1900 (b) second- and third-harmonic levels.
TriQuint’s CuFlip™ flip-chip process enables the high density assembly necessitated by the 5 × 5 mm form factor of the TQM7M4006 PAM. The copper bumps are capped by lead-free solder. This technology has been developed for both GaAs and Si CMOS die. (A typical copper bump is shown in Figure 5.) In addition to size benefits, the Cu bumps also channel heat more effectively and reduce die cost compared to conventional wirebond techniques.

Fig. 5 SEM photograph of a typical copper bump.
Four-layer copper clad laminates and prepreg compose the substrate of the TQM7M4006. The material used in the substrate has a relatively flat dielectric constant in operating frequency range and a low dissipation factor. A fusing test has shown the module can support currents greater than 5A. All via structures are a 200 mm diameter (mechanical drill) that is well suited for high volume production. The metal traces on the substrate form the interconnect as well as transform the impedance of the PA output to a 50 W environment. Both low band and high band PA output matches are two-section low pass in order to suppress the harmonics while contributing to a conversion loss of less than 0.5 dB. The inductor sections of the high band match and RF choke are one layer microstrip line and stripline, while the low band match uses two overlay inductors to reduce loss and minimize the substrate area required.
Both PA die in the TQM7M4006 employ three-stage Vcc control. This creates an operating power range of –20 to 35 dBm (cellular/GSM) and –20 to 33 dBm (DCS/PCS) over the control voltage range (Vramp). The power amplifiers are capable of surviving load mismatches >10:1 at Vramp = 2.2, T = –20°C and battery voltages as high as 4.5 V. Achieving a high efficiency power margin and improved ruggedness is a direct result of employing TriQuint’s flip-chip technology as a foundation for the overall design of this PA module.
Impedance matching is achieved with a single GaAs passive die. TriQuint’s advanced TQRLC process utilizes a thick dielectric resulting in greater precision and robustness with a lower fabrication cost. Thick metallization provides superior quality, a factor that is critical to leading edge PA efficiency performance. Two RF matching capacitors are designed-in per band, while the passive die also includes DC blocking capacitors and a large RF bypass capacitor. Figure 6 shows the passive die.

Fig. 6 The passive die.
The third-generation Silicon Vcc Controller Chip design used in the TQM7M4006 provides band gap reference voltages for both power amplifiers, in addition to band selection and TX enable functionality. The small size of the PMOS pass transistor located on the CMOS die and its associated low voltage drop is a result of an optimized analog CMOS process.
Assembly of copper bumped die has key advantages over existing wirebond and solder-based flip-chip assembly techniques. Plated bumps allow for smaller module size when compared with chip and wire technology. This is not only good for the handset manufacturer, but also allows for a greater number of modules to be processed on a single assembly strip, thus reducing the per unit assembly cost. Furthermore, copper pillar bumps reduce the number of processing steps by using the existing infrastructure for solder-based flip-chip assemblies. The caps of the copper post are dipped in flux, placed on a module substrate and reflowed in a single line operation. This allows for placement of die and chip components at the same time. Throughput is improved by eliminating the separate die attach, cure and wire bonding steps required for chip and wire assemblies.
In operation, the CuFlip copper pillar height (when coupled with the smaller die sizes typically encountered in RF applications) eliminates the need for a separate underfill operation. Underfill material is injected under the die during the overmold process allowing all die on an assembly strip to be processed in a single operation. This has the added benefit of eliminating the ‘keep out’ zone around die that is required for dispensed underfill processes. Taken together, these gains result in a packaging technology that cuts final assembly costs through a reduction in the size of the product and the capital equipment required for manufacturing.
Conclusion
The TQM7M4006 5 × 5 × 1.1 mm quad-band GSM power amplifier module represents a breakthrough in size reduction and demonstrated RF performance. A number of technologies were developed concurrently to achieve this breakthrough ahead of other module makers serving the GSM handset-manufacturing marketplace. TriQuint’s unique CuFlip technology, high performance InGaP HBT PA die, low cost passive process and novel use of four-layer substrates combine to provide an attractive solution for phone designers who face board space limitations. While this module breaks new ground, showing how innovative engineering and imaginative design can leapfrog generations, it also demonstrates that the downward size evolution of RF front-end modules continues. As the market seeks more creative solutions for handset manufacturers, the TQM7M4006 PAM has clearly given designers looking to pack more performance and features into smaller areas of PCB real estate a revolutionary choice for a quad-band GSM PA module.
TriQuint Semiconductor,
Hillsboro, OR
(503) 615-9000,
www.triquint.com.