

To save time and money, HFSS 3D electromagnetic-based virtual prototyping is replacing the classical build-and-test design. By generating high accuracy, physics-based models, HFSS improves engineering productivity, reduces development time and better assures first-pass design success. The high performance electronics industry counts on HFSS™ to provide precision virtual prototypes for high frequency and high speed components. With the introduction of HFSS v10, Ansoft once again provides significant productivity gains to its existing microwave/RF customer install base, while expanding electromagnetic co-design to a new segment of engineers working in the areas of EMI/EMC, optics, RF/analog IC and multi-gigabit designs.
Expanding Electromagnetic Co-design EMI/EMC
In version 10, the HFSS dynamic link has been expanded to SIwave,™ thereby increasing the range of analyses that can be addressed through EM simulation to include EMI/EMC applications. In typical EMI/EMC applications, a designer must determine how a printed circuit board will influence other electronic components in the same housing and how the entire configuration then radiates to its environment. The overall problem requires generalized EM simulations of field interactions and radiation pertaining to the containment housing and its environment, along with simulations of complex, real-world PCBs. These diverse structures are addressed by HFSS and SIwave, respectively, and can now be combined for comprehensive EMI/EMC analysis through the dynamic link. Ansoft has demonstrated how the radiation fields for a complex PCB computed with a SIwave project can now be imposed on a dynamically linked HFSS v10 model (see Figure 1). This is enough to compute all the desired fields, both inside and outside the housing. As a result, the simulated radiated fields are easily compared with EMC standards. New capabilities in HFSS post-processing allow users to perform emission testing by plotting the maximum electric field at a specified distance over a range of frequencies for comparison against EMC regulations. Options support the evaluation of electric fields based on a sphere (as specified in regulations) or cylinder, to replicate measurement set-ups. Furthermore, HFSS post-processing supports scaling these results by the spectrum of the digital signal. Together, the latest versions of HFSS and SIwave can resolve EMC issues in software so that designs comply with FCC limits from the start.
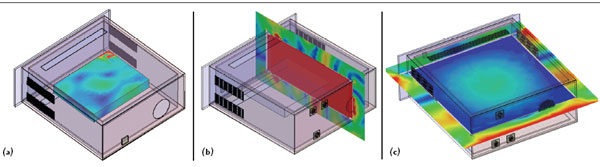
Fig. 1 EM fields derived from the SIwave solution (a), vertical cross section of the E-field surrounding the chassis (b) and the horizontal cross section of the E-field (c).
Optics
For designers of optical components who need to accurately characterize the scattering from these complex geometries, new enhancements to HFSS v10 include post-processing for the automatic calculation of the transmission and reflection coefficients of periodic structures such as frequency selective surfaces and the calculation of monostatic and bistatic radar cross sections. Additionally, new sources have been added, including Gaussian beams, Hertzian dipoles and elliptically polarized incident plane waves making HFSS even more robust for simulating component designs in the optical domain.
RF/Analog
Ansoft introduced the powerful, 3D EM-circuit-system dynamic link in previous versions of HFSS and Ansoft Designer/Nexxim. With HFSS v10, the dynamic-link capabilities between HFSS and Ansoft Designer/Nexxim are further enhanced. The dynamic link allows parametric HFSS component models to be incorporated within Ansoft Designer/Nexxim for EM-accurate circuit and system design and optimization.
For IC designers, this means that 3D simulation of the full layout of critical IC radio blocks is now possible as the performance of HFSS and computer platforms continue to advance. Rigorous simulation of all high frequency layout effects, like on-chip inductors, interconnects, coupling between on-chip passives and substrate coupling, allows issues to be addressed before a costly tape-out. As an example, HFSS v10 simulated the layout of an entire VCO block, excluding all active elements and MOM capacitors. The 142-port HFSS project was solved on a dual-processor PC in the course of a business day, requiring 2.15 GB of RAM (see Figure 2). From the resulting data, the VCO negative resistance exceeded the range for oscillation when the full-block parasitic extraction was included and a design change was therefore required.

Fig. 2 Layout of VCO block simulated in HFSS. Results dynamically to Ansoft Designer/Nexxim for circuit and system analysis.
Multi-gigabit Designs
For designers of high speed interconnects, incorporating parameterized 3D EM component models from HFSS directly into a circuit and/or system simulation through the Ansoft Designer/Nexxim dynamic link is important to accurately address channel performance at multi-gigabit data rates. The dynamic link between HFSS and Ansoft Designer/Nexxim provides a means to investigate time-domain metrics, such as inter-symbol interference and eye closure, with the necessary broadband model accuracy offered by HFSS. The real power of dynamic-link technology, however, is the ability to perform extremely accurate ‘what-if’ analyses, in both time and frequency domains, for a variety of layout and design modifications as characterized by HFSS.
Productivity Gains
High end electronics continue to push the envelope of design complexity and speed, placing increasing demands on HFSS to address growing design size and intricacy. Meanwhile, market demand calls for faster design throughput. The latest release of HFSS addresses structures of increasing geometric complexity and size through several new features, such as new geometry processing technology and advanced meshing techniques, as well as by leveraging expanded processing power.
New CAD Import Features
For HFSS users, the ability to re-use third-party CAD models and EDA layouts saves engineering time and allows designers to spend more time optimizing performance. HFSS v10 introduces features to enhance the quality and reliability of engineering re-use of CAD and/or EDA design through unique auto-interactive model healing and resolution and fault-tolerant meshing algorithms (see Figure 3). These capabilities address anomalies that might occur between solid models used for manufacturing and those used for electromagnetic extraction, allowing for more robust design translation and extraction.

Fig. 3 Imported layout anomalies readily detected and resolved in HFSS v10.
Model Healing
New geometry-translation technology has been implemented to allow for automatic or manual healing of CAD models on import. This technology increases the success rate of design re-use and subsequent simulation, characterization and optimization. A new user interface provides for the automatic realignment or removal of geometric artifacts based on user-specified criteria.
Model Resolution
Developed to simplify the mesh where geometric details are not electrically significant, model resolution enables the surface triangulation to be “scaled-back.” This approach accordingly populates the mesh in areas where there is excessive geometric detail (such as manufacturing screw holes, etc.) that are not significant to the overall electrical behavior of the design. This intelligent, mesh-electrical-awareness approach results in smaller overall mesh construction and faster run times while maintaining HFSS assured accuracy.
Fault-tolerant Meshing
New algorithms have been developed to complement geometry translation so that third-party CAD files cannot only be imported, but also meshed and solved with minimal user intervention. The new fault-tolerant meshing addresses such issues as object overlap and geometrical inconsistencies. New capabilities support mesh-generation feedback to the solid modeler, a graphical user interface to perform validation and integrity checks, and improved geometry fault feedback. Specifically, mesh-based model resolution provides the following:
- Improved mesh quality and reduced mesh size for geometrically complex models, thereby shortening simulation run times.
- Increased speed of mesh generation.
- Automatic and user-configurable.
- Intuitive, easy-to-use controls.
Expanded Processor Power
HFSS v10 also speeds analysis time with the introduction of distributed analysis and support for Windows XP Professional x64 and Redhat Linux 64. The distributed analysis option applies parallel computation toward the investigation of parametric design variations, saving overall analysis time while maximizing the use of existing computer hardware. This optional capability supports the splitting of multiple predefined parametric design variations and/or frequency points, the solving of each instance on a separate machine and then the reassembling of the data, thereby dramatically decreasing the time it takes to solve large parametric and/or broadband designs. The Windows XP Professional x64 version speeds simulation time by providing more direct memory access and reducing the need for hard-disk memory swapping.
Conclusion
The growth of HFSS for the characterization and design of high performance electronic components, from waveguides to antennas, to on-chip passives, to high speed interconnects, serves as a testament to the time and money saved by virtual prototyping. The latest version of HFSS continues to set the pace for solving complex, high performance electronics and new applications for its customers.
Ansoft Corp.,
Pittsburgh, PA
(412) 261-3200,
www.ansoft.com