
Today’s test and measurement suppliers face ever-increasing pressure to deliver more cost-effective solutions to users. They strive for higher production rates while producing products with greater complexity. They are therefore being challenged to supply flexible, scalable and efficient test systems that solve these problems. Synthetic instruments that “synthesize” the stimulus or measurement capabilities found in traditional instruments through a combination of software algorithms and hardware modules that are based on core instrumentation circuit building blocks are a promising solution.
In order to deliver the promised flexibility and modularity of synthetic test systems, Aeroflex has developed the Synthetic Multi-function Adaptable Reconfigurable Test Environment—SMART^E™ 5000 Series—a synthetic test environment that encompasses hardware, software, test practices and support required by users for a complete test solution. This synthetic test system provides a highly integrated, complete-solution environment and includes configurable modules encompassing the best hardware to solve test challenges.

A synthetic test system utilizes multi-functional stimulus and response measurement hardware channels tightly coupled with digital signal processing software (rather than a collection of dedicated-function instruments) to generate signals and perform measurements. Synthetic test environments offer low total cost of test, greater throughput and typically take less than half the rack space and weight of conventional discrete instrument-based systems.
The new system is based upon the fifth generation evolution of the company’s synthetic test technology, which meets the high throughput, high-performance test requirements for radar applications, satellite payloads and transmit/receive modules and subsystems for phased-array radar antennas. In this fifth generation, the proprietary synthetic-test chassis has evolved into commercial off-the-shelf (COTS) LXI modules that support multiple vendors and multiple industry standard platforms (LXI, PXI, cPCI, GPIB).
SMART^E’s configurability enables systems to be properly scaled in terms of size, function and cost for manufacturing, flight line, and depot test for military prime equipment test solutions. The environment also features system declassification of embedded facilities now mandated for most military systems. Modularity and multi-vendor component and subsystem support, along with the ability of synthetic subsystems to adapt to new requirements via software, give users obsolescence protection. This environment is provided using COTS system components to ensure that users have a competitive test solution best matched to their requirements. Furthermore, the extensive application of industry standards in the composition of the environment ensures that test solutions will fit well into the user’s operating environment. Moreover, the user likely will be more familiar with a COTS-based implementation over a proprietary one.
Industry Standard Foundations
A key to the flexibility of SMART^E is its foundation of industry standard software, including Windows, C/C++/C# and National Instruments’ TestStand. The open architecture combination of both industry standard software and hardware enables multifunctional extensions that can be easily implemented.
An extensive test library, with built-in test personality customization via user-settable/exposed parameters, results in rapid start-up for new applications. The test environment embodies all of the calibration, verification, diagnostics and test practices needed to achieve its specifications, which are given at the system level, rather than simply as a collection of instrument specifications that must be analyzed and then extrapolated to the system level.
This focus at the system level includes a multi-tiered calibration practice based on calibrating procedures required for very few, basic transfer standards without the need to remove and calibrate each individual synthetic module or each separate subsystem. Calibration encompasses full National Institute of Standards and Technology (NIST) traceability. All systems are designed to enable system verification tests, even with a unit under test already connected to the environment and ready for testing. Each system also provides simulation software that enables test programs to be run off-line from the system hardware, while still being able to step through all the test sequence elements as if hardware were connected.
From a key subsystem perspective, the systems are constructed of the following building blocks: stimulus, response measurement, system calibration, signal routing and signal conditioning, system controller and software as well as a system infrastructure subsystem. Figure 1 shows the generic block diagram of a SMART^E 5000 environment test solution.
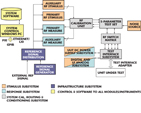
Configuring Test Hardware
Test requirements come in a seemingly endless variety. The one constant is that the test environment should be applications driven and able to deliver the specific levels of performance required. Devices to be tested dictate the number of simultaneous stimulus signals and the range of frequency, power and modulation of the stimulus signals required.
The specifications and test strategy dictate the measurements and therefore the measurement instruments required in terms of both function and performance. The combination of the DUT test signal requirements and the characteristics of the measurement instruments dictate the calibration and signal routing and conditioning components of the system.
Stimulus Subsystem
A stimulus subsystem can encompass a wide variety of combinations of digital, analogue and RF/microwave “channels.” Digital and analogue capability is typically provided in PXI/cPCI form factor, RF and microwave functionality in PXI or LXI form factor. However, conventional rack-mounted instruments may also be utilized in cases where they provide the best match to the measurement problem, though usually not the best modularity of implementation. Figure 2 shows the components of an LXI version of a SMART^E RF/microwave stimulus channel.

Response Measurement Subsystem
Like the stimulus subsystem, the response measurement subsystem of a SMART^E can encompass a wide variety of mixed-signal capabilities from DC to microwave. As for the stimulus subsystem, system module components in PXI/cPCI, LXI or discrete instrument form factor may all be utilized in concert. Figure 3 shows the SMART^E 5000 RF/microwave response subsystem
Common modular instrumentation capability is available off the shelf for digital multi-meters, digital sampling oscilloscopes, arbitrary waveform generators, digital IO and a variety of other measurement functions. PXI/cPCI and LXI and response measurement subsystems may each consist of one or more channels, which may be optionally configured for tuning speed, power level and frequency range. These include UUT interface subsystems, UUT power supplies, system infrastructure, digital IO subsystems and industry standard PXI synthetic instrumentation modules.

Calibration
In the deployment of synthetic microwave test systems, Aeroflex has engineered a very specific hierarchical calibration strategy involving three distinct levels of calibration: primary calibration, operational-reference-plane-origin calibration and extended-reference-plane calibration. This hierarchy is specifically designed to minimize the overhead and maximize the convenience of calibration and verification on a system level basis.
Primary calibration is related to the components of the system responsible for establishing the most fundamental stimulus and measurement parametric behavior of the system. The RF/microwave elements of the system include the reference frequency generator, noise source, power meter and power sensors, S-parameter calibration kits and a core calibration resource known as the Local Calibration Unit (LCU).
For low-frequency stimulus, a high-performance PXI DMM may be the primary reference standard, easily removed for periodic calibration. The LCU facilitates the second level in the calibration hierarchy for RF/microwave signaling. It is the point at which all system resources are integrated to provide a fundamental reference plane origin for both RF/microwave stimulus and response signaling. The LCU provides signal multiplexing to DUT test ports and to industry standard NIST traceable power calibration instruments.
System Infrastructure Components
System infrastructure components refer to components generally required to make the various individual subsystems operate as an integrated environment. In some instances, these may be provided by the user’s application environment. The SMART^E 5000 family provides for required or optional infrastructure components such as an LXI module sub-rack, system racks with AC power infrastructure including uninterruptible power supply, cooling, EMI shielding, system reference signal generation and distribution modules, LO distribution modules, system interconnect cable assemblies, LAN interface router and UUT interfaces.
Test capability can be configured to match the test problem to be solved and the environment also enables expansion or reconfiguration of a system to meet new requirements, providing test resource investment longevity and significant immunity from obsolescence.
SMART^E Specifications
Reflecting its RF/microwave-centric test perspective, the SMART^E features synthetic stimulus and measurement channels to 40 GHz in configurable modular bands with two synthetic channels as standard, one for stimulus and one for measurement, extendable to multiple parallel stimulus and multiple parallel response synthetic or non-synthetic channels. A highly configurable baseband encompasses cooperative narrow and broad bandwidth capabilities and includes very fast tuning or lower speed/reduced cost local oscillator options with AM, FM, PM and arbitrary modulations.
Also featured are standard power settings and a measurement range of –90 to +10 dBm to better than 0.1 dB resolution, extendable via standard and custom power amplifier options. Standard and customer-specified switch matrix subsystems and interface panels are supported. The system provides continuous wave and pulsed measurements—S-parameters, envelope, peak and average power, spectral, noise figure and modulation/demodulation—with network analyzer comparable uncertainties at high throughput measurement rates.
The test environment is application-specific for satellite payloads, phased-array T/R modules and subsystems/assemblies, and multi-device under test military ATE platforms, as well as specific military-tester/ATE implementations for EW and radar range applications. Specialized tactical air navigation (TACAN), identification friend or foe (IFF), CNI and ATE subsystems as well as phase-noise test subsystems are available as system options.
The SMART^E 5000 test environment provides for mixed-signal testing (including DC response), digital input/output (I/O) up to 400 MHz at double data rate (DDR) and low voltage differential signaling (LVDS) with programmable levels up to 100 MHz, low frequency analogue stimulus and measurement from a broad selection of modular or conventional instruments including arbitrary waveform generators (AWG) at gigahertz sample rates digitizers up to multi-gigahertz sample rates, and defense wavelength division multiplexing with variable sample rates up to 1.8 GS/s.
Conclusion
SMART^E 5000 test environments are scaleable in performance and function, ideal for implementing configurable and reconfigurable systems that provide flexibility and resistance to obsolescence, and are a vast improvement on historical rack and stack test solutions. A single synthetic stimulus and measurement channel pair can perform the tests that traditionally require multiple standalone instruments. Thus, there are savings in size and weight requirements for a complete microwave test solution. The result is a unique, state-of-the-art, synthetic, and mixed-signal RF and microwave test environment.
Aeroflex Test Solutions
Instruments Division
Stevenage, UK
+44 (0) 1438 742200
info-test@aeroflex.com