A new range of seamless waveguide sections for sub-mmWave/terahertz (THz) frequency bands have recently been developed by Flann Microwave Ltd. Both 1 in. and 2 in. sections designed for operation at these frequencies have been manufactured using proprietary techniques. A selection of these sections in the WM-380-band (500 to 750 GHz) have been tested at the U.K.’s National Physical Laboratory (NPL) where they were measured electrically using a vector network analyzer (VNA) calibrated using NPL’s primary reference standards. The results were benchmarked against measurements of equivalent devices in this waveguide size from another manufacturer representing the industry standard. They were also compared with modeled results calculated using reference values of resistivity for the waveguide conductor as a benchmark representing the “ideal” case. The results demonstrate the successful manufacture of these sub-mmWave/THz waveguides and their suitability for applications operating at these frequencies.
With the increasing uptake of THz technologies for many applications,1,2 there is a need for high-quality, reliable electrical components operating at these frequencies to support such applications and, in turn, to enable new possibilities for these technologies. Rectangular metallic waveguide is commonly regarded as the transmission line of choice for systems operating above 110 GHz. Its relatively low loss and mechanical robustness offer advantages over other transmission media. The narrow bandwidths often considered a drawback for waveguides at microwave frequencies, do not apply to sub-mmWave/THz waveguide frequency bands. Advances in instrumentation,3 the standardization of waveguide dimensions up to 3.3 THz,4 the standardization of waveguide interfaces5 and improvement in the manufacturing techniques for precision waveguides have led to a proliferation of waveguide devices, components and systems for frequencies above 110 GHz.
However, the increase in operating frequency creates challenges. Smaller waveguide aperture dimensions require tighter manufacturing tolerances; the inherent loss of higher frequency signals emphasizes the need for high conductivity materials and smooth waveguide walls, along with well-matched connection interfaces. The demands of a given application may impose further challenges such as weight reduction or resilience to environmental conditions.
Manufacturing in this field is still maturing, as is the metrology for assessing the success of this manufacturing. Until recently, the manufacture of precision sub-mmWave/THz waveguide components has been limited to the small subset of manufacturers who rely on the traditional split-block construction technique. In addition, the first inter-laboratory measurement comparisons for scattering parameters of waveguides operating in the sub-mmWave/THz bands were conducted only recently.6,7

Figure 1 Flann 1 and 2 in. seamless WM-380 waveguide sections.

Figure 2 (a) WM-380 measurement setup at NPL. (b) Flann 2 in. section connected to VNA during measurement.
Over the past year, Flann Microwave has developed a seamless design for waveguide components in sub-mmWave/THz bands.8 This design features a seamless electro-formed thin wall structure made of copper. The manufacturing process achieves an internal surface finish of less than 0.2 µm roughness average (Ra). For strength, the waveguide itself is enclosed in a stainless steel outer tube. Straight sections, bends and twists can be made using this technique, with expected performance comparable to precision-machined split-block waveguide. The reduced mass and bulk have the potential to provide advantages in many applications. A set of these sections for the WM-380 band is shown in Figure 1. Waveguides in this band feature nominal aperture dimensions of 0.38 x 0.19 mm and are extremely challenging to manufacture successfully.
In this article, these waveguide sections are benchmarked using electrical measurements made at the NPL. Through this benchmarking exercise, the electrical performance of the sections is compared against the current state-of-the-art and the modeled “ideal” case. This allows an assessment of the success of the design and manufacture of these new waveguides, along with their suitability for use in the field of sub-mmWave/THz technology.
ELECTRICAL MEASUREMENTS
Measurement Setup and Calibration
The NPL WM-380 measurement system uses a pair of Virginia Diodes, Inc. (VDI) extender heads connected to a Keysight PNA-X VNA. This test setup is shown in Figure 2a. The 2 in. Flann waveguide section is shown in more detail in Figure 2b. After thermal stabilization of the system, the VNA is calibrated using the primary reference standards for the WM-380 band9 using a 3λ/4 TRL calibration routine.10-12 For the benchmarking exercise, the calibration was performed in 0.5 GHz steps across the 500 to 750 GHz frequency range.
Devices Under Test and the Measurement Process
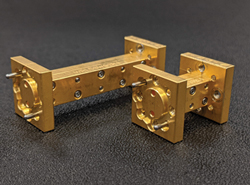
Figure 3 VDI 1 and 2 in. reference DUTs.
The Flann seamless WM-380 sections were measured on the calibrated system. To benchmark these sections against the existing state-of-the-art, sections of equivalent length manufactured by VDI were measured. These sections are shown in Figure 3.
As is evident from the figures, there are distinct differences in the section designs from the two manufacturers. In contrast to the Flann sections, the VDI sections feature square rather than circular flanges and the waveguides have a split-block construction rather than seamless. The VDI design incorporates a thick, rectangular wall structure in contrast to the thin, cylindrical design of the walls of the Flann sections. Both feature IEEE 1785.2a style flanges.5 The devices were treated in the same way during the measurement process.

Figure 4 Measured S11 reflection coefficient magnitudes for the Flann and VDI sections.

Figure 5 Measured |S21| for the Flann and VDI sections.
Measurements at THz frequencies are generally more prone to errors as compared with measurements at microwave frequencies. To address this, a rigorous measurement procedure was followed to achieve reliable measurements. The measurement setup and process was optimized as part of good measurement practice at these frequencies.13 These steps include optimizing the VNA sweep settings, limiting cable movement, handling devices appropriately, using inner alignment dowels to achieve good connection alignment and using a calibrated torque driver to ensure adequate, uniform torque was applied to all screws during each flange connection.
COMPARISON OF ELECTRICAL MEASUREMENT RESULTS
S11 Reflection Coefficients
The measured |S11| magnitudes of both the 1 in. and 2 in. sections are shown in Figure 4. As can be seen in Figure 4, all four sections produced very low reflection results, with |S11| measuring less than -20 dB. There is very little to distinguish the reflection performance of the Flann and VDI devices. An assessment of the |S22| results showed similar performance to |S11| for all the devices. These reflection values are sufficiently small to ensure negligible impact on the transmission loss of each device.
S21 Transmission Coefficients
Transmission coefficients are a key performance parameter for these newly developed waveguides as they indicate how successfully the sections can transmit the signals. The measured |S21| results of both sections are shown in Figure 5. Note that the drop in transmission observed around 750 GHz and more noticeably around 560 GHz is common to all the measurement results. These drops are due to atmospheric absorption peaks at these frequencies.14 The signal loss is due to absorption by water vapor present in the air inside the waveguides. If the waveguides operate in non-atmospheric conditions, such as in space, they will not suffer from these effects. The plots shown in Figure 5 demonstrate close agreement between the Flann and VDI |S21| results for both the 1 in. and 2 in. sections, typically agreeing to within 0.06 dB or less.
The Flann and VDI sections’ performance is close enough that the devices can be considered equivalent. This benchmarks the Flann sections successfully against the state-of-the-art. The slight differences can be attributed to factors like differing waveguide wall smoothness, mismatch levels with the test ports, waveguide conductor resistivity and the repeatability of the connections.
FURTHER ANALYSIS
Dissipative Attenuation
The attenuation response of a 2-port device can be divided into two components. One is associated with mismatch and the other with energy dissipation in the device.15 Splitting the two components this way allows the losses due to conductor effects like surface roughness and finite conductivity to be isolated, removing the effects of mismatch due to imperfect flanges. This allows the results to be compared more effectively with the modeled attenuation of a waveguide section of equivalent length.
The equation used to calculate the dissipative component of attenuation is given in Equation (1):
where S11 and S21 are expressed in linear units.
The modeled attenuation is based on the equation for attenuation constant, α, given in Equation 2:4
where:
ρ = resistivity of the waveguide conductor
ρ0 = reference resistivity of pure annealed copper (17.241 nΩ × m)
a and b = dimensions of the rectangular waveguide aperture in mm (a > b)
fc = cut-off frequency (in GHz)
f = frequency at which α is calculated.
Using this equation, the loss of an “ideal” waveguide with perfectly smooth walls, perfect aperture dimensions and perfectly matched can be calculated for a section of equivalent length with the device under test and with the resistivity of gold.4

Figure 6 Calculated dissipative attenuation results.
The dissipative attenuation was calculated for the Flann sections, with the results plotted in Figure 6. Figure 6 also shows the modeled attenuation for “ideal” 1 in. and 2 in. sections. Note that the modeled attenuation does not incorporate effects due to the aforementioned atmospheric absorption.
For both sections, there is a negligible difference between the measured |S21| values in Figure 5 and the calculated dissipative attenuation results in Figure 6. This confirms the earlier conclusion that the reflection contribution to loss is insignificant. The results for the Flann sections trend well with the modeled results, with what appears to be a systematic offset of between 0.2 and 0.3 dB. We believe this is primarily caused by a higher resistivity for the gold conductor used on the waveguide walls, as compared to the textbook values specified for bulk material samples.4 These values will typically differ from actual material values after the material is machined and electroplated, as often happens during the manufacturing process for high frequency transmission lines. The measured transmission results of the waveguides suggest a higher value of resistivity than used for the model,16 which is also confirmed in this analysis.
Loss Per Unit Length
Loss per unit length is often used to summarize the performance of waveguides. This metric gives a good representation of the loss performance to expect from the practical use of the device. It also allows direct comparison with other waveguide sizes or with other transmission line types. It can be calculated using the mechanically measured length and electrically measured transmission coefficients.16

Figure 7 Calculated and modeled “ideal” loss per unit length results for the Flann sections.
The loss per unit length results for the Flann sections are compared with modeled loss per unit length results, with the results shown in Figure 7. The calculation of the modeled values was performed using Equation (2). A resistivity value of 27 nΩ × m used in this model was chosen to provide good agreement with the measured results. This value compares well with the value of 28 nΩ × m used elsewhere16 for similar devices. The worst-case loss per unit length result for the Flann sections, approximately 0.75 dB/cm, is significantly lower than the 1.1 dB/cm equivalent value given in the manufacturer’s datasheet.8