For 3D bulk dielectric lattices, loaded waveguide/transmission line, free-space methods like focused mmWave/microwave beam and in some cases, the open-ended coaxial probe method are likely the only applicable test methods. For the open-ended coaxial probe, there may be some limitations in using this method for dielectric lattice structures that do not present a flat, uniform face because air gaps will lead to errors. Issues also arise if there are structural elements significant to the desired dielectric performance that cannot be adequately captured within the fringe fields of the coaxial probe.
For loaded transmission line and waveguide approaches, the physical size of the transmission line/waveguide will impose limitations on the measurement frequency range. Here, the tolerances scale inversely with the frequency to ensure adequate measurement accuracy. Free-space methods have limitations on the sample size and the orientation and isotropicity of the sample must be considered when performing free-space methods like loaded transmission line techniques. Free-space measurements are possible at very high frequencies with relatively small samples, but since the sample size of this method scales with the wavelength, this imposes a constraint on lower frequency measurements.
Expert Discussion on Dielectric Measurements
To gauge the prevailing trends and applications the industry is addressing for dielectric structures, the authors interviewed some of the leading experts in the field. The following are excerpts from interviews conducted with these industry experts on complex dielectric structures and dielectric measurement methods.
What are the applications for these dielectric structures?
Marzena Olszewska-Placha, Ph.D., Vice President for Research & Development, QWED Sp. z o.o.:
Most common materials that are tested with test fixtures, which we develop and offer, are sheet dielectrics, semiconductors and conductive composites. Dielectrics typically include electronic laminates, polymers and ceramic substrates such as LTCC and ULTCC materials. Conductive composite materials cover a wide spectrum of applications from EMC/EMI to energy materials, including anodes for battery cells.
Jonathan Chisum, Ph.D., Associate Professor for Electrical Engineering, University of Notre Dame:
Our research focuses on low-cost and wideband beam scanning lens antennas for applications in 5G/6G mmWave wireless communications, satcom and sensing. Emerging commercial and low-SWaP defense applications demand extremely low-cost and low-power beam scanning antennas. Gradient-index (GRIN) lenses support extremely wideband operation (e.g., 8 to 60 GHz in a single aperture) and provide sufficient degrees of freedom that they can be optimized for wide angle beam scanning with high aperture efficiency.1,2 However, they are difficult and expensive to fabricate. Due to recent developments in low loss tangent 3D-printed dielectrics, GRIN lens antennas offer a passive beam scanning alternative to the PAA and, when 3D-printed, are low-cost.
Nico Garcia, Ph.D., CEO & Founder, Cheshir Industries:
We are designing and building GRIN lens antennas, a disruptive technology platform with various applications in microwave and mmWave communications and sensing. Our GRIN lens antenna products are low-cost, power-efficient, ultra-wideband alternatives to conventional beamforming antenna solutions.
John Schultz, Ph.D., Chief Scientist, Compass Technologies Group LLC:
At Compass Tech, we are experts in electromagnetic (EM) measurements, especially dielectric measurements and measurement test systems. We also design specialized antennas and probes. For instance, we recently developed a low frequency antenna technology designed to replace bulky low frequency horns, a metamaterial flat lens antenna. Instead of being 30 to 40 in. wide, like the low frequency horns, it is only 2 in. wide. Another example that we are developing is a flexible, slip-on lens for enhancing probe directivity that we manufacture using a fused filament fabricated (FFF) AM technology. We also manufacture a laboratory focus-beam system that we have available at various frequencies with different lens types and technologies.
How and why are precise dielectric constant and loss tangent figures for a dielectric critical for your application? Do these parameters need to be precisely measured or can they be estimated?
Marzena Olszewska-Placha, Ph.D.:
In the case of QWED, I can answer this question from two perspectives, which are related to company activities. Firstly, from the perspective of a vendor of test fixtures for the precise measurements of dielectric properties. And secondly, from the perspective of a company running various research and development activities related to our expertise in designing a wide spectrum of microwave devices. In the design of microwave devices, where interactions between EM fields and materials are involved, e.g., a microwave applicator for bituminous surface treatment, precise knowledge about materials’ parameters, mainly dielectric properties, often as a function of temperature, is required. The more precise this knowledge is, the higher the effectiveness of a design and final real-life device. This experience is our driving force in our second branch of activities, for developing fixtures for microwave characterization of dielectric properties of materials of various kinds.
Jonathan Chisum, Ph.D.:
To realize these benefits, a GRIN lens requires a continuously varying dielectric constant throughout the lens volume. And, to maintain high radiation efficiency, the dielectric should exhibit very low insertion loss. Since there are no methods by which one can realize an ordinary material with arbitrary dielectric constant, GRIN lenses are realized as artificial dielectrics comprising unit cells with varying volume ratios of air and a background or host dielectric to achieve an effective dielectric constant. A curve that illustrates the effects of the volume fill factor on effective permittivity is shown in Figure 1(a).
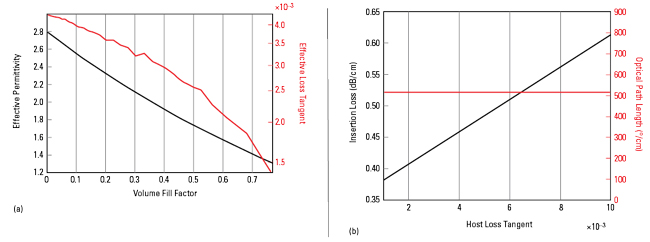
Figure 1 (a) Effective permittivity vs. volume fill factor at 28 GHz. (b) S21/cm vs. host loss tangent at 28 GHz.
Figure 1(b) shows that the optical path length is constant over an order-of-magnitude change in dielectric loss tangent, indicating that phase collimation is insensitive to dielectric loss, but the insertion loss is linear, in dB, with loss tangent. Therefore, it is essential that low loss dielectrics be used and quantified to determine gain from directivity.
Nico Garcia, Ph.D.:
Accurate measurement of the dielectric constants of GRIN materials is crucial. The dielectric constant relates directly to the propagation constant and wave impedance of a GRIN sub-structure; accurate characterization of these parameters is essential to the overall GRIN lens design. Accurate measurement of the loss tangent is less critical assuming that the loss tangent is sufficiently low, ideally around or below 0.002. This is generally easier with alumina and other ceramics, but modern RF composites and laminates are now consistently around this threshold. GRIN lenses generally comprise composite dielectric structures and it is often necessary to take real measurements of these structures’ EM properties before proceeding with design or fabrication. Modern simulation tools are extremely accurate but the simulation model needs to account for manufacturing non-idealities and tolerances; this is only possible if you have real sample measurements on hand with which to compare/tune the simulation model. This step is crucial because GRIN lenses tend to be sensitive to fabrication tolerance. Of course, once you are comfortable with a fabrication paradigm and associated non-idealities, it is sufficient to rely on well-honed simulations. For example, if you are using a relatively simple composite structure like drilled laminates and your manufacturer has excellent tolerances, you may be able to get away without doing any measurements beyond the first round of characterizations. However, if you are working with complicated or unproven structures then high accuracy measurements are essential.
The degree of dielectric precision needed depends on the operating frequency. This is largely because the propagation constant scales with frequency; characterization error of the propagation constant, as a result of characterization error of the dielectric constant, will be exacerbated at higher frequencies. If you design for W-Band or terahertz, you’ll want very precise and accurate EM characterizations only because the propagation constant is so high. Of course, at these frequencies, your mechanical tolerances need to be tighter too because the wavefront will be increasingly sensitive to physical kinks and discontinuities in the structure.
John Schultz, Ph.D.:
For lenses, you don’t want a high permittivity lens, you will get too much reflection. Hence, you need to reduce the permittivity of the lens to enhance overall performance. For practical dielectric applications, such as metamaterial or dielectric lattice structures, you need a pattern with features that are less than a wavelength in order to stay away from resonance. This results in a wide bandwidth structure, which then means you also need to be able to characterize or make measurements of the structure precisely over a wide bandwidth. An approach we have used in the past for dielectric lens development is to make samples with various fill fractions and use the focus-beam system to precisely characterize the complex permittivity of the samples. In this way, we can then take what we know and design a lens with the desired performance.
Conclusion
Additive manufacturing technologies are allowing for even greater degrees of freedom in the design and fabrication of 2D and 3D dielectric structures. Capturing the performance of these structures and being able to predict the dielectric response reliably and accurately is crucial in developing technologies with this new technology. This first part introduced concepts of performing measurements on these new classes of dielectrics. The second part of this article, to be published in an upcoming issue of Microwave Journal dives deeper into these concepts with more from a panel with extensive expertise in dielectric measurement.
References
- J. Baker-Jarvis, M. D. Janezic and D. C. DeGroot, “High-Frequency Dielectric Measurements,” IEEE Instrumentation & Measurement Magazine, April 2010, Web: https://www.nist.gov/system/files/documents/2017/05/09/Baker-Jarvis-IMMag-April-2010.pdf.
- J. Obrzut, “Measurement of Materials Dielectric Properties,” Springer Handbook of Material Measurement Method, September, 2006, Web: https://www.nist.gov/publications/measurement-materials-dielectric-properties.
- J. Krupka, “Frequency Domain Complex Permittivity Measurements at Microwave Frequencies,” Measurement Science and Technology, April 2006, Web: https://iopscience.iop.org/article/10.1088/0957-0233/17/6/R01/meta.
- J. Krupka, “Microwave Measurements of Electromagnetic Properties of Materials,” Materials, Vol. 14, No. 17, Sept. 2021, Web: www.mdpi.com/1996-1944/14/17/5097.
- P. I. Dankov, “Two-resonator Method for Measurement of Dielectric Anisotropy in Multilayer Samples,” IEEE Transactions on Microwave Theory and Techniques, Vol. 54, No. 4, June 2006, Web: https://ieeexplore.ieee.org/document/1618573.
- J. Baker-Jarvis and S. Kim, “The Interaction of Radio-Frequency Fields With Dielectric Materials at Macroscopic to Mesoscopic Scales,” Journal of Research of the National Institute of Standards and Technology, Vol. 117, Feb. 2012, Web: www.ncbi.nlm.nih.gov/pmc/articles/PMC4553869/.
- Broadband Dielectric Spectroscopy.
- C.K. Lee, et al., “Evaluation of Microwave Characterization Methods for Additively Manufactured Materials,” Designs, Vol. 3, No. 4, Sept. 2019, Web: www.mdpi.com/2411-9660/3/4/47.
- E. Costamagna and P. D. Barba, “Inhomogeneous Dielectrics: Conformal Mapping and Finite-element Models” Open Physics, Vol. 15, No. 1, 2017, Web: www.degruyter.com/document/doi/10.1515/phys-2017-0099/html?lang=en.
- M. A. Sitterly, ”Electromagnetic Characterization of Inhomogeneous Media,” Air Force Institute of Technology, March 2012, Web: https://scholar.afit.edu/cgi/viewcontent.cgi?article=2160&context=etd.