Air is essentially the second most useful dielectric after a vacuum from an electrical performance standpoint as it applies to high frequency circuits. Unfortunately, air is a challenging substance with which to fabricate precision structures. The next best option to a pure air dielectric is to build structures using as much air as possible within a dielectric structural medium. This is where high performance dielectric foams come into play. These foams are nearly completely air with a minimal amount of structural polymer, ceramic or glass for physically connecting high frequency structures while minimally impacting electrical performance.
These types of foams are used in high performance advanced antenna system (AAS) panels, radomes, RF windows and many other RF structures where air would be preferred, but structure is needed. Though the effective dielectric constants (Dk) and loss tangents (Df) of these foams is typically good, almost that of air, they present a variety of design and fabrication challenges. Mainly, they are weak to compressive forces, tend to crush during lamination and have no clear and reliable pathway to support high frequency plated-through-holes.
An emerging option, additively manufactured (AM) dielectric foam, is fabricated using advanced 3D printing techniques and new low Dk and low loss dielectric composites. This new method generates dielectric lattice structures that mimic the effect of air-filled foams while providing structure where needed to support selective metallization and mechanical support.
This article aims to educate readers on the state of dielectric foam technology, the challenges it presents to designers and AAS fabricators and how new AM dielectric foam, leveraging 3D printed technology, may provide a pathway to address these challenges.
WHY & WHERE AIR IS BETTER
For low loss and low dielectric constant (Dk) applications, a vacuum is the ideal dielectric. However, in atmospheric applications, maintaining a vacuum is rarely feasible. In atmospheric cases, air is the most ideal realizable dielectric material, with a relative permittivity of approximately 1.00059 at standard temperature, pressure and humidity (see Table 1). This compares to the relative permittivity of perfect vacuum (free space) at precisely 1, by definition. The dielectric loss, or loss tangent, of a vacuum is zero, where air is close enough to zero that it is largely considered negligible.

It is also important to note that the characteristics of air as a dielectric are stable over frequency, even into terahertz frequency ranges. This is particularly attractive, as many other common dielectrics are not stable over frequency, though some are stable over large frequency ranges. This is why air is used to create high Q-factor capacitive coupling structures such as those used in the latest AASs.
The dielectric strength of air at standard atmospheric conditions is roughly 30 to 70 V/mil or 1.18 to 276 MV/m. This is relatively low compared to other dielectrics, which means care must be taken when using air or air-like dielectrics in high-power applications where peak voltages could reach the breakdown point.
DRAWBACKS OF DIELECTRIC FOAMS
To overcome the challenge of structurally supporting electrical and mechanical components of RF systems with air, some type of solid dielectric structure is needed. This is where dielectric foams have carved a niche.1 These foams are typically made from polymers or other dielectric materials that can be reliably fabricated with large pores or gaps (voids) in their structure while still allowing for mechanical shaping and coating/layering. The combination of air and dielectric structure in these foams effectively reduces the overall dielectric constant and loss tangent as a function of the air-to-dielectric volume ratio (void fraction or void ratio). The higher the volume ratio of air, the closer the complex dielectric properties are to air. This is why some dielectric foams can be made with dielectric constants of approximately 1.1 to 1.2 with comparably low loss tangents, as they are mostly air by volume.
It is important to note that the actual effective complex dielectric properties are a ratio of the volume fraction of the material that the electric fields pass through. This makes precise control and conformity of the foam extremely critical, as any inconsistencies in the effective dielectric properties could lead to degradation in the performance of the desired function of the foam, be it for example, an RF window, radome, lens or part of a laminated stack.
A growing use for dielectric foams has been as part of a laminated stack between circuit components and between coupled antenna elements in upper microwave and mmWave AASs. A critical design consideration for these AAS stacks is to minimize the dielectric constant and loss tangent between the coupled antenna elements while still providing structure that allows for precision alignment and fixturing.
Dielectric foams, being mostly air, typically do not have any substantial compressive strength, especially when fabricated as relatively thin sheets needed for AASs. This becomes a substantial fabrication challenge, as compression is needed to laminate sheets into stacks of substrates and electronics. Lamination is also commonly used to add metallic conductive layers to dielectric substrates. In either case, the susceptibility of dielectric foams to compression typically leads to crushing during lamination, where some thickness of the dielectric foam is lost close to where the laminating force is applied, and at fixture/support points as well.
HOW AM MAKES BETTER STRUCTURES
The degrees of freedom and material selection capability enable AM dielectric foam structures to be made with a wide range of dielectric and structural properties that can be designed and tuned for a specific application. In this case, AM dielectric foam can be fabricated to have foam-like/air-like dielectric properties but with superior structural properties. Moreover, an AM dielectric foam can be designed so that areas requiring foam-like electrical behavior are fabricated with the appropriate characteristics, but other areas, such as fixture areas or attachment points, are fabricated in a way that better fits the desired feature performance.
AM dielectric foam can be made to be foam-like in the same way that dielectric foams are designed to be air-like. The concept involves designing the structures to have the volume ratio of air-to-dielectric as high as possible while maintaining the designed structure. Where foams are formed of a multitude of small roughly spherical shells, AM dielectric foam is fabricated using a hollow lattice structure. Traditional AM dielectric foam geometries such as honeycombs or grids are simple examples (see Figure 1).2
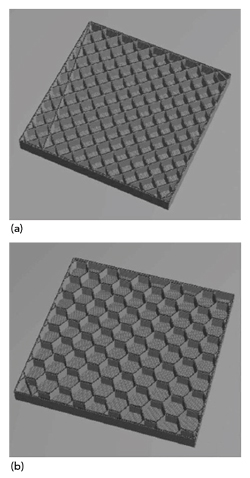
Figure 1 CAD sketches of 3D dielectric substrates with waffle (a) and honeycomb (b) internal structures. Lids not shown.

Figure 2 Luneburg-style GRIN lens constructed of gyroid unit cells using varying wall thicknesses to control the air-fraction and effective permittivity of the “shells” within the spherical lens.