INNOVATIVE OTA TESTING SOLUTION
To address these shortfalls, TMYTEK has developed a phased array antenna testing method that is fast, has a small footprint and measures both power and phase. Since the antenna pattern is a critical element of a phased array antenna, identifying any gain loss or phase differences among elements is important, an aspect that traditional testing methods cannot perform efficiently in production.
TMYTEK’s XBeam system is available in two versions that scan antenna patterns in 2D and 3D in under 10 seconds—100x faster than other commercial test methods. It is compact and fully electronic, with no motors to limit measurements or cause interference. The small footprint makes it easy to integrate with other test elements such as handlers, and its application programming interface (API) and drivers support integration with existing test program configurations. Using TMYTEK’s UD Box up- and down-converter enables use of sub-6 GHz analyzers, eliminating the need for mmWave instrumentation. The innovative hardware and software design enables the system to provide an affordable total cost of ownership (TCO).

Figure 5 XBeam 2D test system.
XBeam 2D

Figure 6 Pattern measurement comparison: XBeam 2D vs. the CATR.
The XBeam 2D is the more economical version of the XBeam family, suitable for production line testing (see Figure 5). It is usually used for the small arrays used in mobile phones or customer premise equipment and also supports 2D testing of larger arrays, such as 5G radio unit and satcom terminals. The XBeam 2D receives and analyze one cut of the beam, generating a 2D pattern at ±5 degrees within 1 second. The radiation pattern is digitized, and the RF power data can be retrieved via the ethernet interface. For measuring other RF parameters, such as error vector magnitude (EVM), the XBeam 2D can be connected to a spectrum analyzer or universal auto tester via a 2.92 mm connector. The small box measures 30 × 15 × 8 cm.
To confirm the XBeam 2D’s measurement quality, TMYTEK tested and compared the XBeam 2D with a CATR under the same conditions using the mmWave New Radio beamforming development tool, BBox. The results (see Figure 6) show the peak gain and radiation patterns are similar, sometimes equal, whether the beam is at boresight or offset to a steering angle. The data confirms the XBeam 2D’s measurement method and results agree with the results achieved with a CATR.
A key feature of an AiP is beam steering, which has a baseline with all elements or channels having equal gain and phase. The OTA measurement system should be able to detect variations among the channels, which may indicate failures or the need for system calibration. To illustrate XBeam 2D’s ability to identify such issues, a 1 × 4 channel AiP module was measured with channels 1 and 2 purposefully adjusted for 3.5 lower gain and a -60-degree phase offset to simulate a defect. Figure 7 shows the measurement results, comparing the failures and good sections under the same test conditions. A single horn measurement system, which only measures peak gain at 0 degrees, would be unable to screen the non-functional components. By performing a full 2D pattern scan, gain differences can be noted when channel power is lower and the specific channel identified. With the phase offset, the beam has clearly shifted, and the AiP unit can be flagged by the test system.

Figure 7 Measurements showing low gain and phase offset effects.
TMYTEK XBeam 3D
XBeam 3D extends the measurement capability to two dimensions, e.g., azimuth and elevation. The system comprises a specially designed shielding box and the TMYTEK BBox radio detector head in a 50 × 50 × 50 cm testing cube (see Figure 8). This first-generation module tests 28 GHz systems across ±50 degrees in 10 seconds.

Figure 8 XBeam 3D test system.
The software developed for XBeam includes:
- BeamPicasso™, which measures beams at various angles
- mmWatson™, which measures and identifies faulty AiP modules
- OTACali™, which efficiently calibrates a phased array OTA.
The software can transform parameter measurements into visual bitmaps (see Figure 9). Piece-by-piece calibration and statistical analysis matures the database, improving the capability to identify defects accurately and quickly.

Figure 9 Parameter maps generated by the software engine.

Figure 10 Demonstration measurements of the XBeam 3D integrated with auto tester.
To further improve capability and flexibility, handler APIs supporting popular wireless tester drivers enable the XBeam 3D to be fully automated in a mass production test system. Figure 10 shows test results with the XBeam 3D integrated with one auto tester. Gain and EVM were measured at three beam angles in under 2 seconds, with the beam pattern analyzed in real time to identify failures, so defective components can be flagged. Testing speed enables the measurement data to be collected and fed to a database for artificial intelligence (AI) modeling and intelligent analysis, correlating production batches with the characteristics of array elements, for example. Real-time processing improves production efficiency and provides feedback to design engineering teams.
Like the XBeam 2D, the 3D cube can be customized for testing different modules with various form factors and operating frequencies based on the same testing approach. Both version of XBeam are software driven and powered by AI. Table 1 summarizes the capabilities of the 2D and 3D versions of XBeam, and Table 2 compares the capabilities of XBeam to the CATR and horn antenna testing configurations.

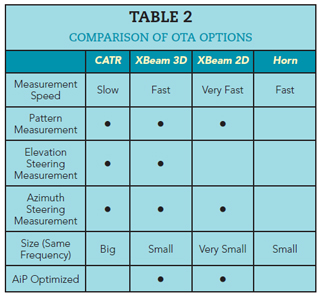
SUMMARY
The AiP is a key architecture for mmWave systems and devices, and the XBeam 2D and 3D test solutions offer a comprehensive way to test these systems. They can evaluate system performance—antenna patterns, EIRP, EVM—with the efficiency needed for production environments. Test times are typically 100x faster than can be achieved by traditional methods. With up- and down-conversion, the XBeam family interfaces with sub-6 GHz measurement instruments, further improving TCO. The XBeam test modules are compact and compatible with production handlers, and the AI-driven system software helps gain insight into AiP performance.