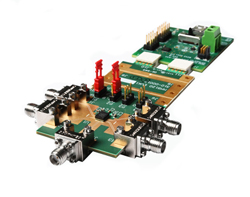
Menlo Micro claims it’s no exaggeration that MEMS technology and its Ideal Switch® have effectively reinvented RF switching. Its MEMS switches, typically mounted in a land grid array package, are orders of magnitude smaller and lighter than electromechanical relays (EMRs). They can handle high RF power levels and operate well into mmWave. They are also highly linear, have minimal insertion loss and are reliable, designed to last more than 3 billion switching cycles without performance degradation.
Menlo Micro’s latest RF switch, the MM5120, exemplifies what MEMS-based switch technology can achieve (see Table 1). The high-power single pole four throw (SP4T) switch operates from DC to 18 GHz and handles up to 25 W CW, 150 W pulsed power to 6 GHz, with an input third-order intercept point greater than 90 dBm. The switch’s on-state insertion loss is 0.4 dB at 6 GHz and it consumes less than 5 mW of DC power, making it well suited for power-sensitive designs and applications such as switch matrices, RF front-ends, tunable filters, antenna tuners, interface boards, digital step attenuators and beam steering in both MIMO antenna arrays and AESA radars.
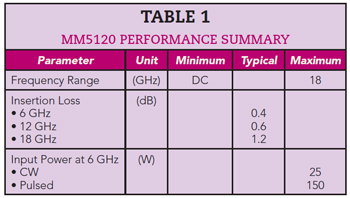
For designers, the MM5120’s features enable switching solutions to be achieved in a small footprint—5 × 4 mm—that formerly required lots of board space and DC power. For example, the low power consumption of the MM5120 means that when deployed in large switch matrices, all the switches will consume less power than a single EMR, while delivering speeds 1000x faster and requiring 90 percent less space.
Menlo Micro’s MEMS switches are fabricated using through glass via (TGV) packaging, i.e., short, metalized vias. TGVs enable a dramatic reduction in switch size and eliminate wire bonds which reduces package parasitics by more than 75 percent for RF and microwave applications.
While all EMRs employ a metal beam as the actuator, MEMS switch actuators are so small their mass is negligible. This means they can deliver stable, long-term performance when subjected to extreme shock and vibration—harsh conditions in which electromechanical relays fail. The MM5120 and Menlo’s other Ideal Switch devices exceed the IEC 60601/60068 standard and pass MIL-STD 810G/H stress tests for shock and vibration.
Because Menlo Micro’s switches are electrostatically actuated, they need high voltage and low current biasing. To accommodate this, Menlo developed a high voltage charge pump and driver circuit and integrated it with the MM5120 and other Menlo switches. Unlike other MEMS switches, this integration eliminates the need for external components such as a discrete charge pump and driver/multiplexing circuit. Menlo’s integrated high voltage charge pump and controller enables the switch’s SPI and GPIO digital interfaces to control the switch from any host processor.
The technology that made these MEMS switches viable is the result of more than 12 years of research and development (R&D) conducted by General Electric (GE) for the company’s power systems. Menlo Micro’s founders played an integral role pioneering this MEMS switching technology at GE. Recognizing that its switch innovations could benefit multiple industries, GE spun out the technology, creating Menlo Micro in 2016. Backed by $225 million in funding, Menlo Micro’s founders leveraged GE’s MEMS and material science R&D to develop MEMS technology with the goal of transforming electronic switching, which led to Menlo Micro’s Ideal Switch.
Ongoing development in collaboration with partners has yielded MEMS switches able to handle kilowatts of power, high temperatures and operating lifetimes in decades. Menlo Micro’s switch portfolio includes models that operate to 40 GHz; new designs will extend the frequency range to 60 GHz.
Menlo Micro
Irvine, Calif.
www.menlomicro.com