Historically, high-reliability (hi-rel) components involved custom and often proprietary processes and were used almost exclusively by the military and space industries. This trend of build-to-print interconnects has shifted in many ways, where it is now more feasible for military and aerospace systems to leverage high-rel commercial off-the-shelf (COTS) components, simply because they often satisfy the electrical performance and physical durability requirements of these systems, frequently with the added benefit of interoperability. This article provides an overview of the trends in high-rel COTS coaxial assemblies, as well as covering the general construction of high-rel cables.
The last decade has seen growing demand for COTS devices across almost all civil and defense-related platforms (e.g., radar, EW, UAV). This is attributed to the increasing need for multi-platform open architectures to replace legacy systems and newer, rapidly evolving systems. The Government Accountability Office (GAO) - an organization that actively audits, evaluates and investigates federal programs for Congress - has identified large government agencies such as the Department of Defense (DoD), Department of Energy and NASA as high risk organizations, largely due to their “inefficient contracting approaches.”1 The implementation of massive, long-term contracts is no longer desirable, due to the potentially compromising position of excessive spending and long contracts. The military’s buying power is now finding ways to leverage small business and increase competition, in turn enabling more rapid development and highly efficient, robust systems. Notably, overall contract obligations have decreased dramatically in both the defense and civilian sectors: Federal agencies procured 24 percent less in products and services in the 2015 fiscal year compared to 2011.

Figure 1 “Death cycle” of aging military systems, leading to decreased modernization and, ultimately, obsolescence.3
To reduce the total cost of ownership for the DoD, programs have shifted from massive, long-term contracts for custom built, complex systems to acquisition strategies that involve flexible design requirements for incremental advances in complex systems. The DoD’s Reduce Total Ownership Cost (R-TOC) program, implemented in the early 2000s, involves three approaches:2
- Improve reliability and maintainability (R&M).
- Reduce supply chain response time and logistics footprint.
- Establish a competitive supply base to support products.
These goals still hold today, as military procurement is increasingly shifting toward evolutionary acquisition, a method that delivers capability in increments, enabling a stepping-stone path to capability improvements. Contrary to the spiral shown in Figure 1, this shift mitigates the major ownership risk of large operation and support (O&S) costs for aging systems, which invariably moves funds from procurement to maintenance and hurts system modernization.
RF CABLE MILITARY SPECIFICATIONS
Passive subsystem components such as interconnects can often use a COTS-based solution, so long as the assembly ensures the quality and reliability necessary for mission-critical applications. For a coaxial cable, this means that every part of the cable assembly - the center conductor, dielectric, shielding, cable jacket and connectors - has to be considered, as well as the testing to validate reliable performance. Vendors of hi-rel COTS components recommended for military applications establish pedigree through open industry standards involving various levels of stringency. Military specifications (mil-spec) are among the most intensive because of the tracking and transparency necessary for every step of cable fabrication and testing. The MIL-DTL-17 standard for flexible and semi-rigid RF cables is the most exhaustive military specification for coaxial cables, often citing MIL-STD-348 for connector interfaces.
In contrast, the complementary MIL-STD-790 standard ensures reliability through a Qualified Products List (QPL), a system established by the DoD to simplify purchasing products that meet defined qualification requirements. Having a product introduced to the QPL involves two main aspects: lot traceability and compliance to the relevant specification test requirements.
Lot traceability is the ability for a manufacturer to trace all piece part acquisitions back to the original source, as well as the manufacturing processes to fabricate the end product. This is immensely helpful with failure analysis and quality assurance, as the cause of any failures can be readily discovered and future risks mitigated. Naturally, when considering the number of components that go into an assembly, this task can become overwhelming. An effective enterprise resource planning system is likely required, as well as a systematic process to upload all of the information. Moreover, a training program is mandatory to be able to continually produce qualified parts. Figure 2 illustrates the lot traceability process for a coaxial assembly; it has more than 30 steps.

Figure 2 Order processing flow for military grade coaxial assemblies.
The ability to demonstrate that in-house testing adheres to the specification requirements is also critical, as a wide range of conformance tests is necessary for coaxial assemblies. Some manufacturers provide the additional transparency of providing test reports for each lot, as datasheets may only reveal a limited amount of data. While test reports are not necessarily linked to a QPL, the ability to access test plots allows a designer to be acutely aware of the performance of a component.
ANATOMY OF A MIL-SPEC CABLE ASSEMBLY
As stated earlier, two major standards can be drawn upon to understand the materials, interfacing and conformance requirements for a coaxial cable and connector: MIL-DTL-17J and MIL-PRF-39012E. Both of these require repeated testing during nearly every phase of connector and cable fabrication to ensure performance. The traceability of this testing is necessary to qualify a product on the QPL.

Inner Conductor
The dimensions and materials of the various coaxial assemblies used in military installations are predetermined in MIL-DTL-17. Tables 1 and 2 list some of the materials used in RF cables and some of the additional requirements for military purposes. For center conductors, this includes testing tensile strength and elongation of the individual strands in a stranded center conductor prior to stranding, as well as the minimum distance between the individual wire joints. Solid center conductors that are coated with silver will have a minimum coating thickness, while copper cladding will specify a conductivity of at least 40 percent of copper, as specified in the International Annealed Copper Standard.

Dielectric
Mainly three dielectrics are specified: polyethylene (PE), polytetrafluoroethylene (PTFE) and fluorinated ethylene propylene (FEP). These can be installed in either a solid extruded fashion, air-spaced with expanded/perforated/porous tapes or with filament threads that can be braided. Most engineers are familiar with PE and PTFE insulating materials; the FEP material exhibits a similar dielectric constant to PE and PTFE, with the benefit of high temperature performance. This material is often used as the jacket for plenum applications. An air-spaced dielectric incorporates air as the dielectric, which can be accomplished using threaded filaments, foamed or some type of porous tape. Ultimately, this enables a lower dielectric constant and less signal loss. This material also supports smaller cable diameters.
Shielding
The shielding of a military standard cable can be either braided or solid tubes. For the braided types, the amount of coverage is crucial, as gaps in shielding allow interference and signal degradation. The amount of coverage is apparent by using the equation in the standard. Solid outer conductors will have a standard purity of at least 99 percent, and they can be either seamless or welded. Welded shields, however, must be recrystallized to produce a uniform grain size across the conductor. Often, hi-rel cables involve at least two layers of shields and a barrier tape to prevent signal leakage and interference.
Jacketing
Jacketing plays an important role in the reliability of coaxial assemblies. These materials must undergo various mechanical stress tests to ensure the integrity of the cable. Parameters such as tensile strength, elongation, ozone resistance, oil resistance, brittleness temperature, flammability, abrasion resistance, tear strength and heat distortion are measured - in commercial applications, most of these measurements are not even considered. A fairly broad range of plastics and thermoplastics can be used for jacketing in military applications. A sample list from MIL-DTL-17 is shown in Table 3.
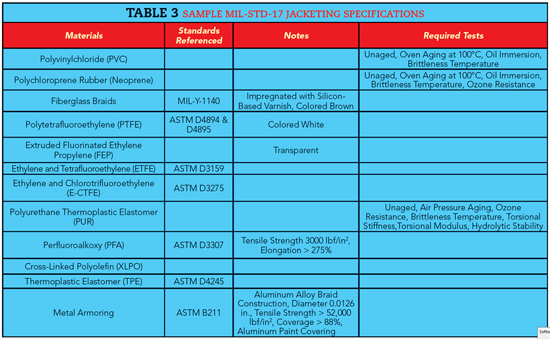
Generally, four types of jacketing materials can be used in a hi-rel cable assembly: thermoplastic, thermoset, thermoplastic elastomer (TPE) and armoring. A thermoplastic (e.g., PVC, PTFE) is a type of material that can be formed above a certain temperature and solidifies upon cooling; it is often formed using an extrusion process. A thermoset (e.g., neoprene, EPR) is permanently set after the curing process, as the internal cross-linked polymers are very resistant to high heat application and have considerable elasticity. A TPE mixes both these chemical technologies to generate a product that can be molded and remolded, while benefiting from the elongation properties of thermosets. Thermoplastics are typically more conducive to indoor applications, as they are highly manufacturable. Thermosets can handle ultraviolet exposure and aging well in outdoor environments. This is not the case for all thermoplastics, as plasticizers can be added to the thermoplastic to enable properties such as low-temperature flexibility, impact resistance and resistance to chemicals/oils. Armoring a cable enables the assembly to handle mechanical shocks and abrasions, which may be helpful in applications where a large vehicle could run over the cable.
Connectors
The MIL-PRF-39012 standard describes the required visual, mechanical and electrical testing necessary to qualify and inspect coaxial cable connectors, and MIL-STD-348 lists the specific interface dimensions for coaxial connectors. Coaxial connectors have mating mechanisms including bayonet, threaded and push-on. The military standard requires a measurement of the force, or torque, required to engage/disengage the mate. Having a minimum requirement can prevent these connections from becoming unmated under mechanical duress, such as flexure or vibrational strain. It is also prerequisite for dissimilar metals not to be next to each other and for the connector head to be constructed of nonmagnetic materials, as galvanic corrosion can occur due to the electromotive force at a bimetal joint. At high powers, these joints and ferromagnetic materials can be a source of passive intermodulation distortion (PIM). Parameters measured for RF connectors include permeability, leakage (when pressurized), insulation resistance, center contact retention, corrosion resistance and VSWR. The general anatomy of a hi-rel military coaxial cable is shown in Figure 3.

Figure 3 Anatomy of a mil-spec coaxial cable assembly, showing material and construction requirements.
COMMERCIAL- VS. MILITARY-GRADE

Military standards involve procedures to ensure the structural integrity of coaxial cables and connectors through nearly every step of the design process. While commercial-grade coaxial components generally involve tests for insertion loss, return loss or VSWR, bend radius and, sometimes, capacitance, full mil-spec assemblies require many more electrical tests and extensive physical tests and burn-in. Table 4 broadly summarizes the major differences between commercial and mil-spec, hi-rel cables.
While commercial-grade components are generally less expensive to procure, they are not necessarily cost-effective due to the wide variation in quality between vendors. This leads to interoperability issues during installation, as well as failures in the lab or field. Military-grade coaxial assemblies and their respective fabrication processes are more predictable. This characteristic of process quality and individual component reliability has led to COTS mil-spec coaxial assemblies being used in applications beyond military. Without a doubt, both the commercial and military markets have their own sets of pros and cons. Mil-spec, hi-rel COTS components join many of the best aspects of both.
References
- “Contracting Data Analysis, Assessment of Government-wide Trends,” GAO-17-244SP, March 2017, www.gao.gov/assets/690/683273.pdf.
- “Reduction of Total Ownership Costs (R-TOC) Best Practices Guide - Dau,” Institute for Defense Analysis, IDA Document D-2843, July 2003, www.dau.mil/cop/log/DAU%20Sponsored%20Documents/Reduction%20of%20Total%20Ownership%20Costs%20R%20TOC%20Best%20Practices%20Guide%20DTD%20July%202003.pdf.
- H. Demir, “The Performance of Reduction of Total Ownership Cost (R-TOC) Pilot Programs,” Thesis, Naval Postgraduate School, December 2002, apps.dtic.mil/dtic/tr/fulltext/u2/a411582.pdf.
- “Guidelines for Use of COTS Passive Parts in Military Systems,” Naval Surface Weapons Center, Crane Division, July 10, 2003, www.navsea.navy.mil/Portals/103/Documents/NSWC_Crane/SD-18/PDFs/Reports%20&%20Papers/LibraryDodRptPassivesPaperSD18Final.pdf.