Applications of microwave heating are well known and are described in many publications (an exhaustive list of references is given by J. Thuery1). A very promising application of microwave heating in agriculture is to replace toxic, dangerous and environment-unfriendly chemicals used to control vegetation, as described in many articles and patents.2

A major disadvantage of microwave heating in agriculture is its comparatively higher cost, both in terms of equipment cost as well as cost of the energy required for operating the equipment. Inside a domestic microwave oven, the microwave field is contained in a closed resonator and most of the available microwave power is dissipated in a useful way in the food to be heated. On the other hand, unwanted energy losses in an open environment and in the presence of lossy but unwanted targets like soil are much higher in most agriculture applications.
Because of high energy costs, microwave heating may not be competitive with chemicals or with other thermal methods for vegetation control, like direct burning with an open flame. The energy budget of microwave heating can be improved if the shape and polarization of the microwave field is tailored to the particular target. In particular, standing-wave patterns may produce non-uniform results in weed killing. Further, unsuitable polarization of the incident microwave radiation may not induce currents in sensitive parts of the weeds to be killed.
Most experiments described in the available literature mention the use of a single antenna (or a small number of antennas) fed by a single high power microwave source. In the presence of reflections, such a source will generate a standing-wave pattern with deep minima, where the heating effect of microwaves is very low. Unwanted weeds, located in the field minima, will most likely survive such an irradiation. Moving the microwave source on-board a vehicle will only solve the problem of field minima in the direction of motion, while the standing-wave pattern will remain unaffected in the perpendicular direction.
In most agriculture heating experiments, the antenna beam is directed downwards, towards the soil, where most of the incident microwave power is dissipated. The polarization of the microwave field is parallel to the soil surface. Since thin, sensitive parts with small cross-sections of most plants are predominantly vertical, these are heated rather inefficiently in an indirect way.
An efficient microwave source should generate a spatially-incoherent field at least in one horizontal direction, while the source motion solves the standing-wave problem in the other perpendicular horizontal direction. Furthermore, the microwave source should provide at least some vertical component of the electric field to induce currents in thin vertical parts of the plants to be killed. Finally, the design should consider practical constraints, like generating large amounts of microwave power with the parallel operation of a number of small, inexpensive sources.
Horn-antenna Array
A spatially-incoherent field, providing uniform heating, can be generated in many different ways, such as moving the radiating antenna with respect to the target, using separate mode stirrers or using a number of independent, unsynchronized sources. Since a large amount of microwave power had to be generated with a number of small, inexpensive “microwave-oven” magnetrons operating in the 2.45 GHz frequency range, it was decided to operate the magnetrons in an independent, unsynchronized way to generate a spatially-incoherent field at the same time.
Reducing mutual coupling among the single magnetrons is therefore required for at least two reasons: to prevent mutual damage to the magnetrons and to generate a spatially-incoherent field. Mutual coupling of the magnetrons can be reduced in different ways: by designing an antenna array with small mutual coupling among the single elements and by operating the magnetrons in a pulsed way, turning them on sequentially.
The design of the horn-antenna array is shown in Figure 1. The horns are stacked in the E plane and are wide open in the H plane. Such horns have a large phase error in the H plane at the aperture. This phase error can be used to efficiently control the coupling between adjacent apertures, thus allowing a tight stacking of many antennas in the E plane.

Fig. 1 Design of the horn-antenna array.
The dimensions shown correspond to the prototype built for standard magnetrons operating in the 2.45 GHz ISM frequency band. The (internal) waveguide dimensions of 80 × 35 mm were chosen according to the available aluminum hardware and standard waveguide sizes used in microwave ovens. The waveguide width makes a step transition to 200 mm to generate a large phase error on the aperture. By selecting a length d = 52 mm for the wider section, the mutual coupling between two adjacent apertures could be reduced to approximately –25 dB at 2.45 GHz and below –20 dB across the whole 2.4 to 2.5 GHz ISM frequency band.
The practical construction of the horn-antenna array is shown in Figure 2. The wide walls of the rectangular waveguides are made from 1 mm-thick aluminum sheet, while the narrow walls are made from 35 mm-wide aluminum “U” profile. All of the aluminum parts are fastened together with M3 bolts so that the whole antenna can be disassembled if necessary.

Fig. 2 The horn-antenna array.
Since the sizes of the waveguides are close to those used in standard microwave ovens, no particular efforts were required for impedance matching of the magnetrons. Their probes were simply installed exactly in the same position as in their standard application in microwave ovens. Since 12 horns were stacked in the E plane, the whole (active) aperture size amounts to approximately 432 × 200 mm.
A larger number of magnetrons could be used by reducing the waveguide height to less than the current 35 mm. This is desirable, both to improve the spatial incoherence and to make the E-plane radiation pattern of the single horns as wide as possible to increase the vertical component of the electric field hitting the target. Unfortunately, there is no simple mechanical solution to make the waveguide-height transition.
The installation of the magnetrons is shown in Figures 3 and 4. For mechanical simplicity, only straight waveguides were used. These are of different lengths to allow the installation of the 12 magnetrons. The magnetrons used were of the types 2M218 and 2M219K. Both types provide a nominal average output power of 800 W, include permanent magnets, cooling fins for forced-air cooling and RFI filters on the cathode and filament connections. The total average output microwave power at 2.45 GHz is in the 9.6 kW range.

Fig. 3 Installation of the magnetrons.

Fig. 4 The installed magnetrons.
To control the sidelobes of the complete antenna and limit dangerous high power microwave radiation in unwanted directions, some additional hardware is required, as shown in Figure 5. Simple flat metal plates are efficient to stop TE waves on both sides of the array in the H plane. Three chokes, one-quarter-wavelength deep, were installed on each side of the array in the E plane to stop TM waves.

Fig. 5 Radiating apertures.
Power Supply and Operation Monitor
A simple power supply, including a magnetic-shunt transformer, a high voltage capacitor and rectifier, was used for each individual magnetron. Such a power supply allows the operation from a standard 230 V AC, 50 Hz supply, just like any microwave oven. The operation of the magnetron is pulsed with a large duty cycle of approximately 40 percent at the 50 Hz frequency.
Because of the large overall power, approaching 15 kVA, due to the reactive loading of the magnetic-shunt transformers, a three-phase 400 V AC, 50 Hz supply was selected for the whole weed killer with 12 magnetrons. The three-phase power supply was actually an advantage, allowing a simple solution to turn on the individual magnetrons sequentially. The power supplies of adjacent magnetrons are simply connected to different phases of the three-phase supply so that the magnetrons do not operate at the same time. In this way, the operation of the magnetrons is unsynchronized and the resulting microwave field does not form standing-wave patterns with deep minima.
When using a large number of consumer-grade components, like “microwave-oven” magnetrons and corresponding power supplies, component failures are not unexpected. Unfortunately, in the parallel operation of several magnetrons, the failure of a single microwave source may go unnoticed, compromising the result of the experiment. An efficient and reliable monitor of the operation of each individual magnetron was therefore required.
The circuit diagram of the magnetron power supply and corresponding operation monitor is shown in Figure 6. The use of complex and delicate electronic components like microprocessors was intentionally avoided, since these would hardly survive the intense microwave-radiation environment. The monitor circuit simply checks the DC current through the magnetron by turning on an indicator lamp.

Fig. 6 Power supply and operation monitor circuit diagram.
The monitor circuit is inserted in series with the high voltage rectifier. In this way, the magnetron anode and the transformer winding can be grounded in the conventional way. There is no high voltage present on the indicator lamp either. The indicator lamp is a 6 V, 0.2 A, incandescent light bulb and its filament will only turn bright three to four seconds after turn on, when the cathode of the magnetron reaches its operating temperature.
The light bulb is protected from excessive current with a 6.8 V Zener diode, since the magnetron achieves its nominal output power at an average current of 300 mA. The 2200 ?F capacitor averages the current during the pulsed operation of the magnetron. The RF choke is installed close to the socket of the light bulb, so that the latter is not turned on or even destroyed by stray microwave radiation.
There is a total of 12 power supplies and 12 monitor circuits with 12 indicator light bulbs, one for each of the 12 magnetrons, as shown in Figure 7. The power supply components are installed on one side of the waveguide antenna array while the indicator lamps and cooling fans are installed on the other side.

Fig. 7 Power supply components and cooling fans.
The first tests of the assembled high power microwave source are shown in Figure 8. The apparatus was installed upside-down so that the radiating apertures were facing the sky. Two fluorescent tubes were used as simple indicators of the high power microwave radiation. The main purpose of this test was to verify the correct operation of all components and estimate the efficiency of the cooling fans.

Fig. 8 Upside-down operation, testing for stray radiation.
A microwave-radiation meter, Wandel & Goltermann model EMR-300, was used to find safety distances for human operators in different directions. The efficiency of the metal plates and quarter-wavelength chokes around the radiating apertures could be estimated with the same instrument.
Practical Experiments
After the functional tests in the antenna test range of the department of electrical engineering at the University of Ljubljana, Slovenia, the high power microwave source was shipped to the department of agriculture at the University of Padova, Italy, where it is being used by the research group of professor Cesare De Zanche.
The high power microwave source was installed on a small cart. The wheels of the cart are oriented so that the direction of travel is perpendicular to the horn-antenna stack. The orientation of the antenna array is best described on the bottom-view drawing seen in Figure 9. The cart is further equipped with two screws to adjust the height (spacing) of the radiating apertures above the soil.

Fig. 9 Installation of the microwave source on a cart.
Since all of the practical experiments had to be performed in the field, a three-phase 400 V AC, 50 kVA generator was selected as the power source. The generator was driven by a tractor engine, as shown in Figure 10. Surprisingly, the magnetrons and their power supplies survived all of the field test, in spite of the consumer-grade components and the known imperfections of the generator, such as voltage and/or frequency fluctuations.

Fig. 10 First functional tests in Padova.
A practical experiment of irradiation of different weed cultures with microwaves is shown in Figure 11. The cart is pulled over the weed cultures at a precisely-controlled speed using a winch driven at constant rpm. Unfortunately, the wire pulling the cart is so thin that it is almost invisible.
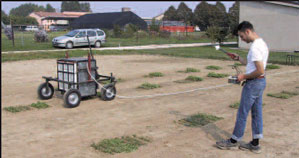
Fig. 11 Microwave weed killer in operation.
The weeds were mainly heated by microwave absorption. However, some taller plants touched the horns and produced arcing and fire. Experiments were made at different speeds of the cart and at different heights (different spacings) of the radiating apertures above the weeds. Stray microwave radiation was monitored with a Holaday model HI-1501 Microwave Oven Leakage Meter at all times for safety reasons. The immediate effects of microwave heating of different weeds are shown in Figure 12. Even in these conditions, some plants may survive. On the other hand, some apparently unaffected plants may die a few days or weeks later.

Fig. 12 Microwave treated weeds.
Conclusion
Compared to an earlier microwave source, with a single magnetron and a single horn antenna used in the experiments by the group of professor De Zanche, the new source provided a considerably more uniform illumination of the target. This is probably due to both the incoherent radiation in one direction (in the E plane of the radiating horns) and moving the source in the other horizontal direction (in the H plane of the radiating horns) above the target.
The early prototype with a single magnetron and single horn antenna was simply positioned over the weeds to be treated. In this way, the horn formed a closed cavity with standing-wave patterns, clearly visible on the heating effects on the weeds. The new source, with 12 unsynchronized magnetrons, was held at least 10 cm or more above the soil, so microwave power could escape on the sides. Nevertheless, the new source provided almost twice the power efficiency; the energy required to kill the same amount of weeds was almost halved.
Furthermore, it was noticed that the efficiency of the new source, with 12 unsynchronized magnetrons, decreased rather quickly by lifting the source higher, from the initial 10 cm up to 25 cm above the weeds. This is probably due to the fact that the vertical component of the electric field decreases much faster than the horizontal component when the distance is increased. Finally, at larger spacings, heating non-uniformities in the form of standing-wave patterns started to appear as expected from theory.
At the time this article was written, the experiments by professor De Zanche’s group were still going on. Although the new source shows an improved power efficiency, the latter still needs to be improved further to be competitive with other forms of weed destruction. All of the current experiments were done at 2.45 GHz, due to the inexpensive magnetrons for this frequency range. Some other microwave or even RF frequencies may be more efficient for weed killing as well as different antenna designs.
Acknowledgments
The author would like to thank Stanko Gajsek and Janez Presetnik for building the prototype of the incoherent, high power microwave source at the department of electrical engineering at the University of Ljubljana, Slovenia. The author would also like to thank the group from the department of agriculture at the University of Padova, Italy — Prof. Cesare De Zanche, Cristiano Baldoin and Werner Zanardi, and Ivan Sartorato of the Istituto di Biologia Agroambientale e Forestale (IBAF) - CNR, for performing many practical experiments with the described microwave source.
References
1. J. Thuéry, Microwaves: Industrial, Scientific and Medical Applications, Artech House Inc., Norwood, MA, 1992.
2. J.R. Wayland, Jr., F.S. Davis and M.G. Merkle, Vegetation Control, United States Patent 4,092,800, June 6, 1978.
Matjaz Vidmar received his BSEE and MSEE degrees from the University of Ljubljana, Slovenia, in 1980 and 1983, respectively. He received his PhD degree in 1992, also from the University of Ljubljana, for developing a single-frequency GPS ionospheric correction receiver. He is currently teaching undergraduate and postgraduate courses in electrical engineering at the University of Ljubljana. His research interests include high speed electronics for optical fiber communications at 40 and 80 Gbps. He is also taking part in amateur satellite projects. He developed very high efficiency VHF and UHF transmitters that were successfully flown in space on the Microsat mission in 1990 and microwave receivers that were successfully flown in space on the Amsat-P3D mission in 2000.