CHALLENGES IN INTEGRATING PASSIVE COMPONENTS
When designing circuits, engineers must balance the use of active and passive components, addressing any integration challenges through thorough testing and simulation. When integrating passive components, one difficulty can be ensuring compatibility among components from different manufacturers, which may impose limitations or specific requirements that must be addressed. Additionally, performance may be impacted by the physical layout and placement of components, necessitating careful design and planning. The potential for electromagnetic interference (EMI) and other environmental factors must be considered in the operation of components. These issues can be addressed with high-quality components.
Another challenge is the trade-off between performance and the costs of performance. Components with the best RF performance may have higher costs or longer lead times. However, optimal performance in passive components can mitigate the total cost of ownership.
There are other common challenges when integrating passive components into electronic assemblies:
- Space Limitations: Size is a factor when designing passive components for electronic devices. Advancements in consumer electronic devices, such as smartphones, have required a high density of components to become smaller and more compact. Fitting passive components into these designs without compromising performance presents a challenge.
- Heat Dissipation: Passive components in high-power applications can generate significant heat. Effective thermal management is essential to prevent overheating and ensure the long-term reliability of electronic devices. Materials and packaging designed to dissipate heat effectively are needed to protect passive components and the device’s effective operation.
- Signal Integrity: A device’s successful operation depends on the reliable transmission of electrical signals. Signal degradation can cause performance issues such as interruptions, distortions or worse, failures, especially in compact assemblies.
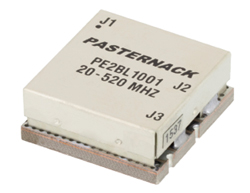
Figure 5 Pasternack PE2BL1001 balun.
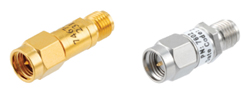
Figure 6 PE7467-10 (gold-plated brass) and PE7602-10 (stainless-steel) fixed attenuator pads.
EMI is one specific challenge in signal integrity. EMI degrades signal integrity by causing unwanted signals and noise. High frequency applications rely on signal conditioning, which can be directly impacted by EMI. This creates a challenge when designing a system architecture that can effectively diagnose and correct signal integrity problems.
Efficient, safe and reliable electrical system performance requires mitigating the challenges presented. Some solutions for these issues include using miniaturized components, implementing advanced materials to improve thermal management and employing precise printed circuit board (PCB) design techniques to minimize signal degradation. Careful component placement is also integral. Figure 5 shows an example of a broadband surface-mount balun, operating from 20 to 520 MHz, designed to address some of these challenges.
ADVANCEMENTS IN MATERIALS AND MANUFACTURING TECHNIQUES
The continuous evolution of passive components in manufacturing is critical to keeping up with the technological advancements of a competitive market. Materials and manufacturing techniques have significantly enhanced the performance and reliability of passive components. Figure 6 illustrates how the same function can use different approaches. Both devices are 10 dB fixed attenuator pads with SMA connectors but operate at different frequencies. The operating frequency of the gold-plated device is DC to 12 GHz, while the stainless-steel device operates from DC to 6 GHz.
Some of the advancements being made in the design and manufacture of passive components include:
- Materials: Advanced ceramics and composites have improved the high frequency performance and durability of passive components. Ceramics, in particular, are valuable for their insulating properties. Specific ceramic materials, such as those having piezoelectric characteristics, are easy to manufacture in various shapes and sizes. This helps fulfill the need for miniaturization in passive components. Composite phase change materials enhance heat dissipation by creating heat transfer pathways for components. These materials offer superior electrical properties, thermal stability and mechanical strength, making them ideal for high performance applications.
- Manufacturing: 3D printing has enabled the fabrication of complex electronic passive components at a lower cost and weight. It also allows for more precise and smaller components essential for modern compact electronic devices. 3D printing overcomes the limitations presented by PCBs in manufacturing, enabling the creation of complex geometries and leading to components with improved performance and functionality.
- Thin-Film Technology: The primary advantage of thin-film technology in electronic components is its ability to control electrical properties precisely, enabling miniaturization and enhanced performance. This manufacturing technique involves depositing thin layers of conductive or resistive material onto a substrate. Common passive components produced using thin-film technology include resistors, inductors, capacitors and filters. Thin-film resistors and capacitors provide higher precision and stability than traditional thick-film components, making them ideal for demanding applications in telecommunications, aerospace and medical devices.
- Integrated Passive Devices (IPDs): IPDs consolidate various passive components, such as resistors, capacitors and inductors, into a single unit. This addresses the issues of limited size and signal integrity by reducing the space required for passive components and the length and number of interconnections, mitigating degrading effects.
Innovations in materials and manufacturing processes, such as ceramics, composites, 3D printing and others, have many benefits for passive devices. These materials and techniques enable smaller passive components with improved thermal regulation, better performance at high frequencies and the ability to withstand harsher environments. These improvements enhance the reliability and functionality of microwave components in demanding applications.
Passive microwave components are critical in various advanced technologies and high frequency applications. With emerging system trends and requirements, these improvements are needed more today than with previous generations of these technologies. These systems include:
- 5G Networks: The upgrade from 4G to 5G networks increased the demand for passive components to filter signals in support of additional antenna systems. High frequency passive components, such as filters and couplers, are essential for managing the increased data rates and bandwidth requirements of 5G technology.
- Automotive Radar Systems: Passive components are crucial in radar systems to ensure the reliable and accurate operation essential for safety-critical applications. The transmit and receive sections of automotive radar systems rely heavily on analog component content and depend on passive components to function properly. Passive components like inductors and capacitors are used in radar systems to filter and condition signals, ensuring accurate detection and measurement of objects.
- Medical Imaging: Passive components are vital in the mission-critical medical technology market. These components are engineered to perform reliably under extreme conditions, ensuring the safety and effectiveness of medical devices and equipment. Their enhanced durability, stability and precision make them ideal for critical applications in healthcare settings. Passive components are used in MRI systems to filter and condition signals, ensuring clear and accurate imaging results.
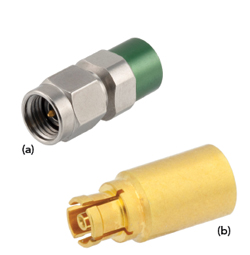
Figure 7 (a) PE6TR1106 2.92 mm and (b) PE6162 Mini-SMP RF loads.
Considering the needs of these rapidly growing market opportunities, companies that design and manufacture passive components are redoubling their efforts. Infinite Electronics brands, such as Pasternak and Fairview Microwave, are expanding their RF passive component offerings to support these applications especially at high frequencies. While these passive functions may seem more straightforward than their active component counterparts, the time, cost and performance-associated risks of improperly selecting the best passive component solution can easily impact system cost, performance and delivery. Figure 7a shows an example of a 2.92 mm RF load and Figure 7b shows a Mini-SMP RF load. Both RF terminations operate to 40 GHz.
Passive components are integral to the performance, reliability and safety of countless devices and systems people depend on daily. These components are indispensable in everyday electronic devices and advanced technology applications, from managing electrical current and storing energy to filtering signals and protecting against voltage spikes. The challenges in their integration, such as size, compatibility, heat dissipation and signal integrity, are met with innovative solutions and advancements in materials and manufacturing techniques. The steady progress and improvement of passive components drive further innovations in applications like 5G networks, automotive radar systems and medical imaging. As more sophisticated and high performance electronic devices are developed, passive components will remain foundational to their effective operation.