Time domain reflectometry (TDR) is particularly helpful in properly measuring and understanding the return loss performance of a connector transition. By time gating, you can examine the loss associated with the connector instead of guessing how much of the total signal chain loss it is contributing. In addition, TDR plots, as shown in Figure 4, can reveal both the location and magnitude of mismatches that occur in the transition regions of the connector interface.
The key consideration is that it is important to know that the usable frequency can often be much lower than you might expect. As a result, you must know exactly what level of return loss and frequency is truly required for the specific application and verify that the connector selected will be able to meet those needs.
ATTACHMENT METHOD
By definition, RF connectors will be making connections between other connectors or transitioning connections to a board or device. When used to transition to a board or device there will be attachment method factors that need to be considered. The connector will need to be both mechanically and electrically attached. Moreover, both the housing ground and the signal pin require an independent electrical connection and how this is achieved has a large impact on the return loss. As a result, the complete attachment strategy is a required factor to consider for any design.
As mentioned, the electrical connection methods used for both the signal pin and ground are important considerations since they will directly impact performance. In many cases, the electrical attachment also factors into the mechanical attachment. The attachment method is one of the critical factors that must be considered for all RF connector selections. It has a major impact on the performance that can be achieved and requirements in this area can also contribute directly to cost. It is also the most important factor when considering the mechanical structure requirements that must be met.
SOLDERING ATTACHMENT
Soldering is one of the most commonly used electrical attachment methods because it is fairly rigid and it also factors directly into the mechanical attachment considerations. However, it is not recommended that solder be the only mechanical attachment or support applied. Although rigid, solder is also brittle and can crack easily, especially if gold plating is dissolved into it. Soldering will expose the connector and the region around it to very high temperatures and connectors must be specially constructed to withstand those temperatures. This will be listed on the datasheet of solderable connectors.
Another important factor to consider is the process capabilities where the attachment will be done. These capabilities will determine the precision of the performance that can be achieved and the consistency of the strength of the attachment. The volume and shape of the solder on the joints are important to control if low return loss is required. In addition, it is important to note that material differences in the construction of the connector may require that the ground and signal pins be soldered in separate operations.
PTFE is a common constituent in many RF connectors and has a much higher thermal expansion coefficient than the metals used in connectors. As a result, it is recommended to carefully evaluate and possibly refine any solder attachment to validate proper accommodations for residual stresses and changes in geometry that may occur during solder processes. It will also be necessary to similarly validate and refine the process based on RF performance.
Soldered RF connectors should also have additional mechanical support provided by surrounding mechanical elements such as front panels, shields or screw connections to PCBs to reduce the risks of cracked solder joints. Additionally, if solder is used to attach a one-piece center pin it is important to verify that the pin remains well captured after the solder process. Connector options with two-piece sliding element center pins or separate elements that are attached after soldering can help alleviate that risk. If cracked solder joints become a major issue, flexible conductive epoxy on one or all of the attachment regions can be a possible solution.
SOLDERLESS ATTACHMENT
There is an increasing number of solderless attachment options becoming available today. These options reduce the process capabilities required to attach connectors and can also eliminate the uncertainty of the attachment impact on electrical performance. Most of these options utilize the mechanical attachment to press and hold the electrical contacts together. These allow more precise control of the contacts made in the transition region and eliminate the issues associated with exposure to soldering temperatures. These options will generally add additional cost and manual attachment labor, but those can be offset by avoiding the issues associated with soldered attachments and increased performance consistency. They are particularly well suited for connectors that operate above 20 GHz since small differences in soldered joints can result in larger performance variations in these smaller geometries.
Depending on the specific attachment included with the connector, it may still be necessary to provide additional mechanical support to ensure that the connector is unable to shift when mating connections are made or if the connection needs to be able to fully support accessories such as power meters, splitters, etc. Suppliers may refer to this option as either solderless or direct-compression connectors.
Some connectors, such as cable adapters, do not need to be connected to boards, but may still require mechanical attachment. Bulkhead adapters fall into this category. The main factor associated here is the space and surrounding geometry available for the attachment. Fortunately, there are quite a few options ranging from flange mounts to bulkhead nuts to help here. Many of these are available directly on the ends of cables to reduce the need for front panel pass-through adapters.
SPACING REQUIREMENTS
Board-level RF connector transitions typically fall into board-to-board or board-to-cable transition categories. In both cases, there will be a desired port count and a finite amount of space in which to fit those ports. When deciding on an RF connector it is critical to ensure the connector selected can achieve the channel density required by the application, allowing enough space for layout, isolation and end-user access.
Board-to-board connectors can be a little simpler in this regard, as their required density is usually just a function of how much layout real estate is available. Whether one can fit an SMP, SMPM, SMP3 or SMPS connection or any of the many proprietary board-to-board options will depend on the total space available, the required board-to-board spacing and how much space is desired between ports for isolation, components, routing and other needs. There is no one-size-fits-all solution, but, the user may get pushed to a connector that greatly exceeds the frequency needed simply to achieve better density.
Board-to-cable transitions have the added complexity of typically being user-facing and influencing product user experience. When it comes to the standard threaded RF connectors, ranging from SMA to 1.85 mm and beyond, the more space one can allow the user the better. With these style connections, if the connector pitch is pushed lower than about 12 mm center-to-center, then the user may struggle significantly with cable installation and applying a torque wrench to the connection, which is a crucial step in the proper use of threaded precision RF connectors. However, the pitch can be set lower in cases where specialty tooling is made available for achieving accurate torque.
By comparison, denser press-in cable connections such as SMPM, MMCX and others can reduce this pitch requirement for usability significantly. In this case, pitches as low as 6 mm are not necessarily out of the question from a usability standpoint.
On the other end of the spectrum, there are a growing number of connector options on the market that group multiple RF connections into single housings and cable bundles. This has long been true of standardized connections like VITA67. But today, there are an ever-growing number of proprietary options from the larger RF cable suppliers. Many suppliers have standardized on a 2.54 mm pin-to-pin pitch. Of course, these tight pitches come with some increased risk for maintaining isolation at the board level, as you sacrifice much of the ability to place shielding between ports. This tradeoff must be weighed on an application-specific basis.
CONNECTION RETENTION
The gold standard for high-performance cable retention is the threaded coupling nut used by 3.5 mm, 2.92 mm, 2.4 mm, and other precision RF connectors. The definitive reference plane structure combined with the high compression provided by the large threads, when torqued properly, can provide undoubtedly consistent and robust retention. However, if space is tight and port density is critical, then the space-hungry coupling nuts are often the first to go. There are also other relevant considerations, such as ease of cable installation, removal and vibration resistance.
The common forms of RF connector retention are:
- Threaded coupling nuts
- Snap-in and press-on
- Quarter-turn coupling nuts
- Jackscrews and jack sockets
Press-in or snap-in connectors, such as SMP and many other similar connection designs, offer a reasonable compromise between space and retention. Instead of using threads, a ring of compressive spring fingers snaps together to retain the connection while providing positive force for the electrical connection using the exterior edges of the spring fingers themselves pressing into the mating bore. In the case of SMP and its subsidiary designs such as SMPM, the connectors are offered with multiple options of retention force, with smooth-bore, partial-detent and full-detent plug options. It is important to note that the higher mate force options almost always come with a significant impact on mating cycle life.
These connection styles have easily understood mating and unmating forces, usually provided in the manufacturer's specifications. While the retention force is going to be much less than that provided by a threaded connection, they can be sufficient for most applications. This can be a benefit if connections need to be easily removed.
There are drawbacks to this style of retention, though. For one, these connectors can be fragile. On some options, the spring fingers of the receptacles are exposed when not mated and can be prone to damage. Additionally, the spring finger retention designs are inherently compliant with the minute details of their mate. Connectors can shift or change position slightly. As a result, connector repeatability is usually noticeably lower than the repeatability of precision-threaded connectors. This also means they are not particularly well equipped for stability in high-vibration environments.
Quarter-turn coupling nuts are another option. These nuts are seen on the popular BNC connectors but they can also be found on custom and proprietary versions of standardized connectors like SMP and others. Quarter-turn coupling nuts are a less common retention method and are not likely to give you the same precision performance that you would see in an equally space-efficient threaded connector. But connectors with this coupling method can be easy to install and perform well in high-vibration environments, where even threaded coupling nuts might be susceptible to loosening.
Finally, there are several proprietary RF connectors, such as grouped or ganged channel count connectors, which use jackscrew and jack socket retention. This is a common cable retention method outside of RF applications. Because they generally only exist for non-standardized RF applications, their space efficacy, retention force and usability will vary from application to application.
MATING CABLE CONSIDERATIONS
RF connectors make the connections required within the signal chain. Nearly all RF signal chains will involve a cable, either at the input or to connect components in the RF chain. Every cable will have a connector on each end and cables may be a large portion of the overall cost of either the signal chain or how it is tested. As a result, the mating cable considerations are another one of the mandatory factors to consider in connector selection. It is important to understand where cables may be required in the signal chain and if there are already defined cables that must be used or connected to.
The cables and the connectors on the ends are governed by the same cutoff frequency and transition performance rules described previously. Since the cables are coaxial, this reduces the transition impacts. In addition, it is important to understand which of the multitude of connector standards are mechanically compatible to mate with one another and which ones strictly require mating within the same standard.
SMA remains the most widely used standard for RF cables. Because of its widespread acceptance and generally robust mating elements, newer precision 3.5 mm and 2.92 mm connectors share the same mating thread and reference plane depths. As a result, SMA, 3.5 mm and 2.92 mm connectors can be mated from a mechanical standpoint, but there are some important caveats.
The first caveat is that the overall RF performance will be defined by the poorer performance of the two mated connectors. Mating an SMA connector to a 2.92 mm cable will not magically elevate the performance to 40 GHz. Second, SMA plug connectors are not manufactured to the same nominal dimensions and tolerances as the 3.5 mm and 2.92 mm connectors to reduce the risk of damage during mating. In particular, the longer length of the plug center pin allowed on SMA connectors can be damaged if not carefully inserted straight in on the axis. This is true of SMA-to-SMA mates as well, but this concern is compounded further by the more fragile air dielectric collet fingers in precision connectors. Precision 2.4 mm and 1.85 mm connectors also share common mechanical dimensions that allow mixed mating. They are also subject to the lowest performer caveat but do not have the same increased risk of damage.
REPEATABILITY AND MATING CYCLES
The repeatability of an RF connector is dependent on the consistency in loss parameters of the RF connection across multiple mating cycles. This is a less well-known performance measure compared to return loss or VSWR, but it is relevant in cases where consistent performance is required even across remates of the connection. Repeatability is particularly important to consider if the application involves connections that are:
- At your point of device calibration
- Broken and remade between calibration cycles
- Broken and remade as part of maintenance or debugging
- De-embedded based on data collected before final installation
Repeatability is often mathematically defined as a complex subtraction between S11 datasets collected before and then after a remate or between each mate and the sample mean. This quantity is expressed in decibels. Equation 2 shows how an S11 repeatability datapoint is calculated as the complex subtraction between two data points at matching frequencies from before and after a remate, and then converted to decibels:
Where:
R represents the real component of an S11 datapoint
i is the imaginary component of an S11 datapoint.
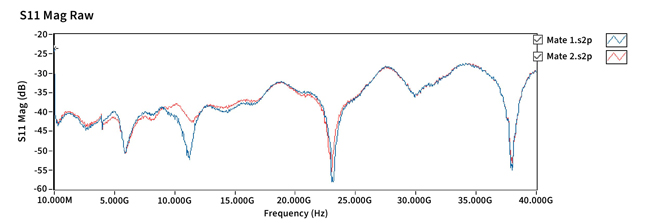
Figure 5a S11 data taken before and after mating.
Like return loss itself, the more negative the value, the better the result. Figure 5a shows an example of two S11 datasets taken on a specific connection pair before and after a remate. Figure 5b shows the complex difference repeatability curve.
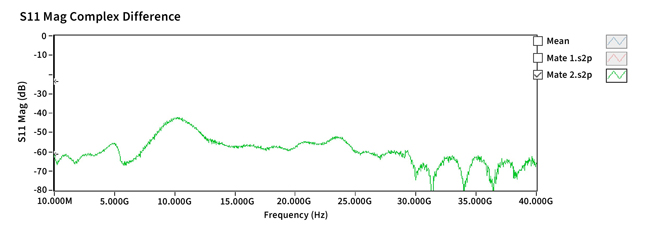
Figure 5b Complex repeatability results.
For most precision connectors, the repeatability performance is defined and bounded by the IEEE 287 standard. This standard can be referenced for more precise repeatability limits of precision connectors, as well as test methodology. The required performance levels vary from -40 dB to as much as -70 dB depending on connector type. Outside of precision connector standards, it is not very common to see repeatability advertised in manufacturer connector specifications. However, some suppliers have data on hand they are willing to share with customers.
The exact repeatability requirements are going to vary greatly by application. Repeatability can be influenced by very subtle aspects of the interconnect, from how well-aligned the connectors are to the effects of concentricity and rotation, to precisely how the slotted fingers or spring fingers settle. For this reason, tightly controlled precision connectors will typically achieve the best repeatability performance, while connections like snap-in and press-on will achieve some of the worst repeatability.
In any application where connections will be repeatedly mated and unmated, it is important to make note of the mate cycle life of the connector choice. This specification can vary significantly between connector styles and even between manufacturers, with some full-detent SMP-style connectors having as few as 100 mates. Threaded connectors and smooth-bore SMP styles may vary from 500 to several thousand, and some proprietary connections have mate lives of over 10,000 mates.
SERVICEABILITY
Serviceability may not be important for most applications but is still worth considering before final selection to eliminate potential costly surprises. To better understand this factor, the specific use case is examined from the perspective of the customer and personnel who will be making connections to the connector over its lifespan. It is helpful to try and answer these questions:
- How likely is damage to the connector?
- How important is the ability to repair the connector?
- Does this repair need to be completed in the field or the factory?
Depending on the answers to these questions, a highly serviceable connector choice may be required. There are connector options that can be changed out directly with little disassembly. Alternatively, an additional replaceable adapter can be applied to the front of a non-replaceable connector to meet these needs. Solderless connectors are not generally field replaceable, but they are much easier to replace in the factory than soldered connectors. All these options will generally add cost to the connection. Answers to these questions can identify the degree of need for a serviceable option. As with the other factors, a balance must be met between cost and requirements.
CALIBRATION REQUIREMENTS
Calibration requirement factors typically only come into play in harsher applications. If calibrated performance is required, then a precision connector choice is recommended. Precision connectors all have broadly available calibration standards and procedures already defined. Additionally, if the connection will be used as a calibration element, then some of the other factors previously described, such as repeatability and transition performance, become more critical.
CONCLUSION
RF connectors fulfill a critical role in virtually all radio and RF test and measurement products and components. Proper selection of an RF connector from the vast variety of geometries available is vital but can be daunting. A methodical consideration of the key selection factors can ease this task. As each selection factor is considered, the choices should quickly narrow to an ideal solution.