
Analysis performed with traditional electromagnetic-field software might give a good sense of the operation of a microwave component from the perspective of pure electromagnetics under ideal conditions. Real-world operating conditions are not ideal, however, and the physical phenomena that affect a component’s performance often go beyond electromagnetics alone—effects from heat, stress and even chemical processes might degrade a component’s performance or even lead to failure. Furthermore, operating conditions could make the retrieval of a malfunctioning component very expensive if not impossible, especially if the device is severely damaged or destroyed. In those cases, other than trying to recreate the problematic operating conditions in the laboratory, the only chance an engineer has to evaluate system performance and determine the cause of catastrophic failure is through software simulation.

A new generation of software features well-proven methods for microwave analysis that engineers can combine with virtually any other type of physics. One such tool, COMSOL Multiphysics, makes this possible by basing its computational engine on the solution of systems of partial differential equations. A well-known example of such a set of PDEs is, of course, Maxwell’s equations—the basis of any computer simulation for RF and microwave design. Multiphysics software can augment Maxwell’s equations with other equations such as those for heat transfer and structural deformation for a strongly coupled simulation. Advanced software tools even allow investigators to start with a clean slate, allowing them to build a physics model from first principles and optionally combine them with ready-made physics models.

Thermal Drift in a Cavity Passband Filter
As an example of a microwave simulation where multiphysics capabilities are beneficial, consider a microwave cavity passband filter exposed to intense sunlight. The result is significant heating and subsequent thermal expansion, which might be large enough to change the cavity’s shape and thus shift its resonant frequency, a phenomena known as thermal drift. This leads to poor frequency stability in the entire system. System engineers need to estimate possible drift in the passband frequency and try to compensate for it.
Figure 1 shows a microwave filter modeled in COMSOL Multiphysics consisting of a box with a cylindrical post centered on one face. It is typically made of brass and is covered with a thin layer of silver to minimize losses. The silver layer is sufficiently thin to have a negligible influence on the device’s thermal and mechanical properties.

The thermal expansion and the associated drift in resonant frequency are caused by a uniform increase in the temperature of the cavity walls. With COMSOL Multiphysics one can readily compute the thermal expansion. Specifically it is the shell template, which handles mechanical structures that are too thin to be explicitly meshed throughout their thickness. Furthermore, the mode analysis of the electromagnetic cavity is done in such a case using the 3D Electromagnetic Waves template in the RF Module, a specialized add-on for COMSOL Multiphysics.
To achieve optimal accuracy, a special method is needed that smoothly deforms the original mesh according to the thermal expansion. The Moving Mesh capability for handling a deformed geometry in COMSOL Multiphysics is used to map the thermal expansion to the geometry used for the electromagnetic wave analysis. This approach accounts for any changes in shape and volume of the domain used for the computation of the resonant frequency. The filter’s temperature can rise due to power dissipation in the filter itself, in the surrounding electronics, or due to external heating. Figure 2 shows the thermal expansion results for a filter made entirely of brass. The original shape is shown as a wire frame with an overlayed exaggerated display of the expansion.

Mode Analysis
Although an actual filter usually consists of multiple cascaded cavities, this discussion limits the analysis to one cell. The cell consists of a thin brass shell with a cylindrical post. Figure 3 shows the filter’s lowest eigenmode. The typical quarter-wave resonance of the cylindrical post is clearly visible. A strong capacitive coupling between the top of the post and the top surface of the box is also visible.
Resonant Frequency vs. Temperature
By repeating the structural and electromagnetic analysis for a number of operating temperatures it is easy to obtain a plot of resonance frequency versus temperature. A comparison of two different designs—one with the entire filter made of brass and one with the post made of steel-appears in Figure 4.
The design with a brass hull and a steel post proves superior with much less thermal drift and hence improved frequency stability for the entire system. The reason is the reduced capacitive coupling between the top of the post and the nearby top surface of the box, which results from the different coefficients of thermal expansion for the two materials. This coupling has a strong influence on the resonant frequency and, when reduced, counteracts the effect of an overall increase in cavity size.

RF Multiphysics Analysis Outlook
Thermo-mechanical-microwave analysis, such as that of the brass-steel cavity filter case just examined, is merely one of many possible multiphysics applications in the RF arena. Other practical examples include the study of surface acoustic wave (SAW) filters and radio-frequency identification (RFID) systems. Computing the frequency characteristics of a SAW filter requires a combined RF/mechanical/piezoelectric analysis where 64-bit solver technology is required to accurately resolve both mechanical and electrical phenomena and possibly also include heating effects. For RFID systems, government regulations require vendors to perform combined RF and thermal analysis to ensure that effects on the human body are below given threshold values.
Intense competition suggests that forward-looking companies involved with research and engineering in RF and microwaves will turn to multiphysics for their modeling and virtual prototyping needs. In many markets such software tools can dramatically slash overall development time, costs and time to market. When working with military and defense systems, though, the stakes are much higher, and so is the need for the most capable tools available on the market.
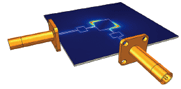
A Simulation Environment for Multiphysics
COMSOL Multiphysics is a finite-element analysis (FEA) modeling environment for simulation of virtually any physical process in 1D, 2D or 3D. Users can model most phenomena through predefined application templates, but they can also modify these templates for very specific requirements or adaptation to the very latest research findings. In addition, optional modules add discipline-specific tools for analysis in the areas of AC/DC, RF and microwave, heat transfer, MEMS, structural mechanics, acoustics, chemical engineering, and earth science. A wide-range of coupled analyses are possible by combining any set of modules. Bidirectional interfaces to MATLAB,® from The MathWorks Inc., and COMSOL Script give access to multiphysics FEA from these programming environments for further optimization, pre- and post-processing. A FEA model can be saved as a MATLAB® compatible M-file and then used to create nested for loops over parameters controlling boundary conditions, materials settings, frequency and CAD geometry dimensions.
RF Module
The RF Module provides tailored user interfaces and solvers for time-domain, frequency-domain and mode analysis for RF, microwave and photonics applications. The user-interfaces support 2D, axisymmetric 3D and full-wave 3D analysis. It can be used for traditional EM-wave simulations such as that of a balanced microstrip patch antenna (see Figure 5) or for strongly-coupled multiphysics applications such as the heating of a potato in a microwave oven where the permittivity and equivalent conductivity are functions of temperature. Figure 6 simultaneously shows the standing electromagnetic wave in the oven and the temperature field within the potato. This particular simulation shows a “hot spot” in the center of the potato.
COMSOL Multiphysics provides a set of automatic and semi-automatic finite-element meshing utilities for the creation of triangular, quadrilateral, tetrahedral, pentahedral and hexahedral vector (also known as “edge”) elements of order 1, 2 and 3. These can seamlessly be combined with elements used for other types of physics.
The ability to mesh assemblies (combinations of CAD parts) allows users to combine different element shapes in the same model, as shown in Figure 7 in a magnification of a meshed part from the aforementioned microstrip antenna simulation.

Using different-shaped element types in different parts of a CAD geometry lets the mesh better adapt to a geometrical shape that, in turn, minimizes the number of finite elements used and thereby speeds up the solution process.
Key Features
COMSOL Multiphysics key features include:
-
Strongly coupled FEA physics simulations: thermal, structural, fluid, chemical, semiconductor and more
-
Bidirectional MATLAB/COMSOL Script interface with automatic generation of M-files
-
State-of-the-art 64-bit meshing and solver technology
-
Moving Mesh for deformable domains
-
User-defined differential equations can be added to an FEA simulation
-
Add-on modules for advanced analysis: Heat Transfer, Structural Mechanics, AC/DC, RF, Acoustics, Chemical Engineering, MEMS, Earth Science

RF Module key features include:
-
3D and 2D frequency-domain and time-domain simulations
-
Material properties can be complex valued, anisotropic, discontinuous, frequency dependent, time dependent
-
Perfectly Matched Layers (PML) for wide frequency band truncation of the computational domain
-
Couples seamlessly with any COMSOL Multiphysics Module.
COMSOL Inc.,
Burlington, MA (781) 273-3322,
www.comsol.com.
RS No. 301