The growth in high frequency applications, driven by satcom, 5G and aerospace and defense, continues to challenge the design engineering community. Challenging RF filter designs continue to escalate with more stringent specifications coupled with the need to reduce the research and development cycle time, sustain RF performance and maintain manufacturing quality.

Figure 1 Mode chart for a cylindrical waveguide resonator.
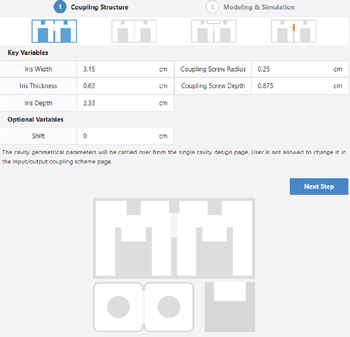
Figure 2 Interface for defining the coupling structure.

Figure 3 Interface for defining the input/output port.

Figure 4 3D modeling screen.
One time-consuming operation in RF filter design is creating 3D models. For companies venturing into new design capabilities or with requirements for completely new geometries, their design engineers are faced with a lengthy development process to produce models and simulations from scratch, followed by extensive optimization. Many available tools use templates to ease this process. Once designers have created a library of designs, this resource is sufficient to support the business for the near future. However, as applications expand to higher frequencies and address new market requirements, particularly at mmWave frequencies, this practice can be hard to scale.
SynMatrix, the RF filter design platform, has released several functions and features during the past two years to help designers accelerate the RF/microwave filter design process. This year, SynMatrix released a significant upgrade to the platform: launching a function that automatically creates 3D RF filter models in Ansys HFSS. This automatic 3D modeling feature supports coaxial cavity filters, rectangular waveguide filters and cylindrical waveguide filters.
One of the highlights of this new function is the design approach, which uses first principle design to build a flexible and highly customizable workflow for any filter application using a specific 3D geometry. This enables the designer to produce and simulate designs in an accelerated workflow.
WORKFLOW FEATURES
The user-guided workflow provides the following features:
Mode chart analysis for waveguide — Waveguide modes describe the field patterns for the waveguide structure. SynMatrix analyzes the transverse hybrid modes, either TE or TM, to determine the widest range of dimensions that will meet the desired operating bands. Through this mode chart analysis tool, users can quickly retrieve the correct waveguide dimension to obtain the widest spurious-free window (see Figure 1).
Single resonator design and analysis — The design workflow begins with a single resonator. SynMatrix supports various coaxial resonators with different shapes. It also handles frequency and Q analysis; dimension synthesis; mode chart analysis for waveguide, including tools to help define the best dimension; temperature drift analysis; and single click auto simulation and modeling. Users can edit the HFSS simulation setup, including refining the mesh.
Coupling design and analysis — SynMatrix features a flexible coupling scheme definition to help customize the coupling structure. For coaxial cavities, SynMatrix supports four major coupling schemes and up to 42 different geometries. It also supports key variable parametric analysis to analyze the coupling coefficient (see Figure 2).
Input/output design — For waveguide filters, SynMatrix offers different waveguide sizes to customize the port interface. For coaxial cavities, the platform supports three major coupling schemes and up to nine different geometries. Like the previous steps in the workflow, parametric study analysis for the key variables is available (see Figure 3).
Full 3D modeling generation — The latest version of SynMatrix introduces a click-and-drag graphical interface to help users fully customize a topology. Unlike other platforms in the market, which use template-based methods, SynMatrix gives users full command and control to build and modify the design. This feature supports generic modeling with different rotation angles. Another highlight, the 3D model generated in Ansys HFSS is fully parameterized. Users can edit the design easily after the model is generated (see Figure 4).
Fast optimization — Once the 3D model is created and simulated using this workflow, users can use the powerful optimization tools available in SynMatrix. The initial performance can be quickly tuned using computer-aided tuning tools and then optimized with SynMatrix’s intelligent optimization suite, which includes automatic AI optimization, space mapping algorithms and the perturbation system.
For Ansys HFSS users, SynMatrix is the only platform that offers a powerful tool for 3D RF filter creation. Other tools in the market use template-based methods to build 3D models, which reduces the flexibility and customization when designing new RF filters. Simplifying the creation and simulation of a 3D RF filter model from scratch can help startups and system companies add new capabilities, build new products and create revenue opportunities. Other benefits include reducing filter component costs, shortening the design cycle time, increasing the design flexibility and efficiency and eliminating dependence on third-party suppliers, which can add risk to a project or solution proposal response. Because the design approach used by SynMatrix is based on first principles, the tool is “future proof” for evolving design requirements. Users can use the workflow knowing the investment will pay back for many years.
SynMatrix Technologies, Inc.
Toronto, Canada
www.synmatrixtech.com