Monopulse (or simultaneous lobing) radars quickly gained popularity after their 1943 introduction by the US Naval Research Laboratories. Their principal benefit - the ability to obtain complete range, bearing, azimuth and elevation angle information from the return of a single pulse - is very appealing in applications such as fire-control tracking and missile control. Today nearly all radars serving these applications are of the monopulse variety, since other types require more pulses (and thus more time) to produce this information and no type can produce it all. However, in order to obtain the highest resolution from monopulse radar, components in the signal chain must control phase, amplitude, insertion loss and ripple to tolerances far in excess of those encountered in typical microwave applications. The FMP Series PC board-mountable IF filters designed for this application are phase and amplitude matched over an IF bandwidth to a reference standard with an unusually high level of precision. The performance achieved by the filters can be applied to other applications in which precise phase and amplitude matching are critical.

The importance of the FMP Series stems from their placement in the IF chain of the radar. Filters with poor phase and amplitude matching, high insertion loss, high ripple, or low phase linearity, will significantly reduce the radar's resolution and degrade its overall performance. However, even tiny variances in these characteristics can noticeably reduce performance, which necessitates the need for extreme precision in the IF filters as well as all other components in the signal path. To understand why this is so, it helps to have a basic understanding of how monopulse radar works.
TABLE 1 | ||
Parameter |
Normal |
FMP Series |
Lead length on coils (mm) |
±1.5 |
±0.5 |
Shunt capacitor values (%) |
±5 |
±0.3 |
Shunt capacitor placement, |
±1.3 |
±0.05 |
Coupling capacitor height |
±0.25 |
±0.025 |
Length of Ruthroff transformer leads (mm) |
±1.5 |
±0.13 |
Placement of Ruthroff transformers, |
±3 |
±0.05 |
Cavity height (mm) |
±0.5 |
±0.13 |
Allowable staking materials |
many |
one |
Orientation of coils |
not critical |
exact |
All Data - From One Pulse
Monopulse radar produces a narrow circular beam of pulses at a high pulse-repetition rate. Each pulse is divided into four signals of equal amplitude and phase that are radiated at the same time from each of four feedhorns grouped in a cluster. The energy from the feedhorns is focused into a beam by a microwave lens, and then transmitted into space. Energy reflected from targets is refocused by the lens (where a phase inversion takes place) and sent through the feedhorns. The magnitude and phase of received RF energy each feedhorn receives varies according to the position and vector velocity of the target relative to the beam axis. The received beams include a sum channel, a difference signal between the upper and lower halves of the antenna, and another difference signal between the left and right halves of the antenna. Through combinations of the sum and both difference channels, any single beam can be compared against the others. Processing of these channels produces the complete range of information about the target. The quality of information derived from this processing can be only as high as the relative precision of the channel paths, and thus the FMP Series filters help to ensure accurate target information.
TABLE 2 | ||
Parameter |
Filter 1 |
Filter 2 |
Impedance ( |
50 |
50 |
IF output (MHz) |
30 |
75 |
1 dB bandwidth (MHz) |
8 |
5.8 |
3 dB bandwidth (MHz) |
- |
9 |
Insertion loss (dB) |
3.3 |
5.0 |
Relative rejection (dB) |
36 at 15 MHz |
38 at 65 MHz |
SWR (max) |
1.30 over ±3 MHz | |
Ripple (dB) |
0.1 P-P over ±3 MHz | |
Phase linearity (°) |
±4 over ±3 MHz |
±2 over ±2 MHz |
Phase/amplitude |
-44 over ±2 MHz | |
Temperature range (°C) |
-55 to +71 | |
Size (mm) |
61 x 10.5 x 10 |
35 x 15.5 x 12 |
Weight (g) |
30 |
25 |
*Phase and amplitude match defined as ratio in dB of the vector addition to the vector subtraction of the signals from two filters, one of which is a reference standard. |
Hand-hewn Precision
Like every microwave filter (and many other microwave components), the FMP Series devices are optimized to deliver their highest performance through a combination of discriminating material and component selection, and tuning by engineers with years of filter tuning experience. However, the stringent tolerances to which these filters must adhere require precision that exceeds that of nearly all other applications. For example, the capacitors used in the FMP Series are selected by a process that eliminates as candidates up to 99 percent of each production lot of devices in order to select those with characteristics that will ensure parasitics can be kept to within ±0.3 percent. This is also typical of the inductors as well as other components in the filters. More of these stringent tolerances are compared to standard filters in Table 1 .
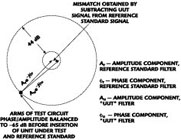
To reduce the internal impedance of the filter by a factor of 4:1, a wideband toroidal impedance transformer is used. This transformer, first described by C.L. Ruthroff in 1959, allows the inductors to be four times smaller than standard designs would dictate, and provides superior decoupling performance, isolating the inductors from both their surroundings and themselves. The Ruthroff transformer, which is far from a well-known commodity to most design engineers, was nevertheless a significant breakthrough that has solved transmission line impedance transformation problems ever since. It involves summing a direct voltage with a delayed voltage that traverses a single transmission line, and provides an inherent high frequency cutoff that is invaluable in the monopulse radar application. In addition to the amplitude and phase matching, the FMP Series filters have high levels of rejection, very low ripple, low insertion loss and high phase stability. All of these specifications, and others, are shown in Table 2 .
Although the filters described here have IF frequencies of 30 and 75 MHz, many others can be specified. Figure 1 shows the match measurement made at a single frequency. In addition, other parameters can be varied to meet the requirements of specific applications, as can configuration and connector types.
Trilithic, Indianapolis IN, (317) 895-3600, www.trilithic.com. Circle No. 301