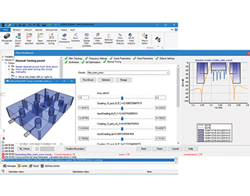
Mician’s Filter Workbench tool is a quasi-automated filter synthesis add-on to the company’s μWave Wizard line of products. Capable of designing and optimizing various physical realizations of microwave filters with moderate relative bandwidths, the tool supports a wide variety of filter designs, from simple waveguide iris filters to more complex geometries such as cross-coupled combline filters. To meet the filter’s RF performance requirements, the user can choose tuning coupling elements manually or using an automated mode. The interface provides real-time visual feedback showing the performance as well as a 3D geometric view of the tuned structure.
EASY SETTINGS
When launched, the Filter Workbench guides the user through synthesis setup, beginning with selecting a suitable filter topology from a drop-down list. Simultaneously, the physical layout for the topology is shown in an information panel next to the input data template, populated with electrical and mechanical parameters for the filter. Different tabs for these entries appear in succession, enabling the designer to proceed to the next tab when all required settings have been entered in the previous tab. While actively editing tabs, explanatory windows provide guidance based on the user’s parameters. If an active tab is incomplete or incorrect, the user’s attention is directed by a red cross at the top of the tab, which changes to a green check mark once all required fields have been filled out correctly. With the final tab populated, all relevant design inputs such as frequencies, cavity and port parameters and default settings have been entered.
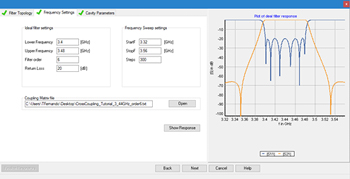
Figure 1 Setting the frequency range, return loss and order of the ideal filter.
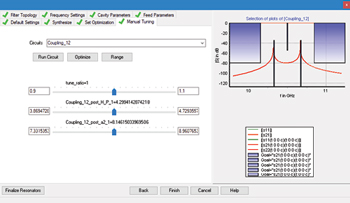
Figure 2 Tuning individual coupling elements.
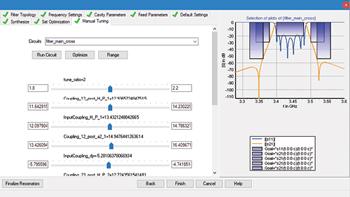
Figure 3 Performance of a synthesized combline filter meeting all specifications.
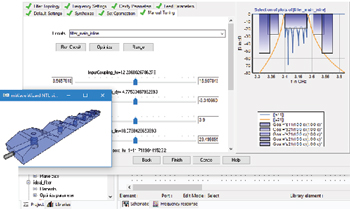
Figure 4 Custom filter design.
After the filter topology has been selected and the corresponding input mask populated, the required parameters for the ideal filter and frequency sweep settings are entered into the “Frequency Settings” tab. Alternatively, an externally generated coupling matrix in a text file can be imported. Selecting the “Show Response” preview option displays the ideal filter response with options to modify the frequency settings, which immediately changes the displayed preview (see Figure 1).
After the frequency entries are complete, the “Cavity Parameters” tab appears. Data entered on this tab immediately returns information such as the cutoff frequency for the specified geometry, recommended iris thickness (if applicable), recommended resonator diameter for highest Q (if applicable), λ/4 wavelength and the estimated average resonator height. For combline filters, surface conductivity can be accounted for when determining the cavity Q factor, which will be displayed as the “unloaded Q.” This value should closely match the Q used for generating the coupling matrix; otherwise, modifications to the cavity geometries may be necessary. For faster computation, the filter synthesis assumes ideal conducting surfaces. At the conclusion of the synthesis, material parameters can be modified in μWave Wizard to account for limited surface conductivity.
Coax port dimensions are defined in the “Feed Parameters” tab, offering the choice between inductive or capacitive input probes. Based on the port geometries and material parameters, the input port impedance is automatically calculated and displayed. For filters with non-coax input ports, the Feed Parameters tab is disabled.
After the filter topology has been specified, optimization control parameters and physical units can be defined. Modifications to the geometry units affect all input values in all tabs, and project default dimensions for geometry units will be overwritten. Discretization and cutoff settings are initially disabled; once the synthesis based on the initial setup is completed, both options will be enabled, allowing modifications.
SYNTHESIS
After completing the filter synthesis inputs, Filter Workbench generates an initial filter model using an automated process for determining the initial dimensions for the center frequency and bandwidth. The resulting 3D full-wave model closely resembles the final filter design. In successive steps, this model is used to finalize the coupling element and resonator geometries to meet filter specifications by automatically dividing the model into smaller circuits, each one an individual coupling element (see Figure 2). After completing the initial filter model, tabs for manual or automated fine tuning of the coupling elements appear. At this point, final changes to the tuning goals can be introduced.
Although the filter response of the preliminary model is usually close to the desired performance, Filter Workbench can be used to refine the individual geometries until the filter meets all specifications. The user can choose between template-assisted manual tuning or fully automated fine tuning. In the “Manual Tuning” panel, individual coupling elements can be selected from a drop-down menu and the coupling elements embedded in tuning circuits. The “Run Circuit” command analyzes the selected tuning circuit and displays the actual performance versus the tuning goals. Relevant iris dimensions of each tuning circuit are represented by tunable variables. With the help of sliders on the Manual Tuning tab, the geometries can be decreased or increased from their initial values, manually optimizing the selected circuit until tuning goals are met. After all individual coupling circuits have been manually tuned, the filter response will appear shifted in frequency, because the resonators have not been tuned to account for external loading. This can be corrected by launching the “Finalizing the Resonators” operation.
With the synthesis process successfully completed, a fully dimensioned μWave Wizard filter model with viable physical dimensions has been created, with subsequent adjustments or additional optimizations possible (see Figure 3).
CUSTOMIZED FILTERS
When selecting a “Customized Filter” topology, Filter Workbench supports the design of filters with arbitrary resonator or iris shapes (see Figure 4). The desired resonator or iris can be created and parameterized either using existing μWave Wizard elements or custom elements generated with μWave Wizard’s 3D modeler.
Filter Workbench is ideally suited for casual filter designers or novices with basic knowledge of microwave filter design. The software assists with determining reasonable initial dimensions, then guides the designer to tune the individual components to meet the specifications. Filter Workbench can automatically synthesize a filter with as little user inputs as filter order, bandwidth and return loss. Advanced users can introduce their own topologies and specifications, then have the software provide a physical realization with options for tuning and optimizing. This eliminates the need to create numerous circuits with numerous variables.
Filter Workbench requires an existing installation of μWave Wizard 2020. Evaluation of the filter synthesis tool is free, available by signing up as product tester on Mician’s website.
Mician GmbH
Bremen, Germany
www.mician.com