
Online Spotlight: Exploring EMI Filtering Options
Electronic devices require a reliable source of electricity for stable operations, which is not always simple to deliver due to the potential for devices to be impacted by electromagnetic interference (EMI). EMI is an electromagnetic wave that induces an unwanted signal in an electrical system that can affect operational requirements. EMI can be caused by other electronic devices or it may occur naturally in the environment from lightning and other weather events like solar flares or static electricity. Figure 1 shows four different modes of EMI propagation:
- Interference can enter equipment directly through the cabling. This is conducted interference.
- Radiated interference can travel directly from the source to the affected equipment.
- Interference can exit an EMI source via a cable and subsequently be radiated from the cable to the affected equipment. The cable is a radiating antenna in this instance.
- Interference can radiate from an EMI source and be picked up by a cable entering the affected equipment. The cable is a receiving antenna in this instance.

Figure 1 Four different modes of EMI propagation.
Depending on the severity, EMI can degrade a device’s performance, lead to a malfunction or cause the device to fail, which can be quite problematic for mission-critical electronic devices such as those used in military and aerospace equipment. For example, if someone is using their phone on a plane when they should not be, you cannot take a risk that this will impact airplane controls. You need EMI filtering to ensure it will never be a problem.
However, too often EMI filtering is an afterthought for electronic device designers and they end up needing to retrofit their devices to properly address the issue. Reducing or eliminating EMI is not only crucial to prevent devices from functioning improperly or failing but there are also regulatory requirements put into place by the FCC Part 15 and EU Directive 2014/30/EU that aim to reduce or eliminate EMI for many critical devices. Since EMI filtering is extremely important for many devices, yet seems complex, this article focuses on explaining the details of different methods for protecting electronic devices from EMI.
THE FARADAY CAGE
The ideal way to protect a piece of equipment or circuit from EMI is to completely enclose it in a metal or conductive box. This screened enclosure is called a Faraday cage. Radiated interference is prevented from adversely affecting the circuit because the Faraday cage creates an equal, but opposite, electric field inside the cage. This field cancels out the external electrical field and prevents the electromagnetic energy field from affecting the circuit inside the cage. This is shown, conceptually, in Figure 2.

Figure 2 A representation of a Faraday cage protecting a circuit from radiated interference.
Most equipment requires input and/or output connections such as power cables or signal and control lines. These lines can act as antennae and pick up or radiate interference or introduce electrical noise and radiate it internally onto other wires and circuits. This means a Faraday cage, alone, likely will not be sufficient and some form of low-pass filtering will often be required.
PANEL MOUNT FILTERS
When used in conjunction with a Faraday cage, EMI filters can provide an ideal solution for removing EMI. Rather than blocking EMI like a Faraday cage is designed to do, EMI filters remove or filter out unwanted signal noise. Two types of EMI filters will be examined in this article: panel mount and surface mount.
A panel mount EMI filter is designed so that any incoming or outgoing cables pass through the filters. The desired signal is allowed to pass through the cable into the Faraday cage, unaffected. The higher frequency interference is removed by being passed through a capacitor to the ground, which is the body of the filter and into the wall of the Faraday cage in this case. Essentially, the EMI filter feeds the unwanted signal through the panel while protecting the circuit. This removes conducted interference and this technique is conceptually shown in the illustration of Figure 3.

Figure 3 Panel mount filter removing conducted interference in conjunction with the Faraday cage.
There are several different electrical configurations available for feedthrough filters:
- C Filter: A feedthrough capacitor with low self-inductance that shunts high frequency noise to ground and is suitable for use with a high-impedance source and load.
- L-C or C-L Filter: A feedthrough filter with an inductive element combined with a capacitor. It is commonly used in a circuit with a low-impedance source and a high-impedance load or vice versa. The inductive element should face the low-impedance source.
- Pi Filter: A feedthrough filter with two capacitors and an inductive element between them. Ideally, this type of filter is used where both the source and load impedances are high.
- T Filter: A feedthrough filter with two series inductive elements separated by one feedthrough capacitor that is suitable for use where both the source and load impedances are low. Figure 4 shows the schematic configurations for these different filter types.

Figure 4 The electrical configurations for different types of feedthrough EMI filters.
APPLICATION CONSIDERATIONS FOR PANEL MOUNT EMI FILTERS
When considering the appropriate filter design, several other variables beyond selecting the appropriate electrical configuration for a panel mount EMI filter must be evaluated. These include the materials, capacitor construction and mounting techniques. The next section explores these factors in more detail.
Dielectric Material
Different dielectrics offer varying performance. This is because dielectric constant stability and therefore, the filter capacitance, can fluctuate with changes in operational and environmental characteristics such as temperature, applied voltage or age. This is important because reducing capacitance also causes the insertion loss performance to degrade.
Different common dielectric materials used for panel mount EMI filters and some of the key characteristics:
- C0G/NP0: Generally unaffected by temperature, voltage, frequency or time because they are very stable. Dielectric constants are relatively low, in the range of 10 to 100 and energy density is low, which means lower capacitance.
- X7R: Relatively stable over temperature, voltage, frequency and time. Typical dielectric constants are on the order of 2000 to 4000, enabling far higher capacitance values for a given capacitor size when compared with C0G/NP0 materials.
- Z5U/Y5V/X7W: General purpose materials, but performance under applied voltage may be seriously compromised.
The characteristics of these dielectrics are summarized in Table 1.
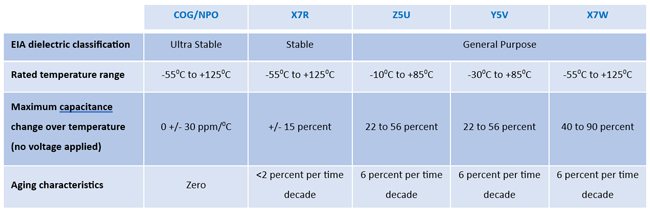
Table 1 Summary of dielectric characteristics
Capacitor Construction: Tubular, Discoidal or Planar
Historically, single-layer tubular capacitors were used for panel mount filters. An example of tubular capacitor construction and the electrical configurations is shown in Figure 5. A major advantage of using a tubular capacitor is that it is very easy to construct a Pi filter in this configuration. But as performance demands have increased, higher capacitance values are required, which means filter designers are starting to use high K, unstable dielectrics and multilayer tubes to form tubular capacitors. However, unstable dielectrics can result in poor performance over the voltage and temperature ranges. In addition, the thin ceramic walls make these capacitors prone to cracking, which results in electrical failures.
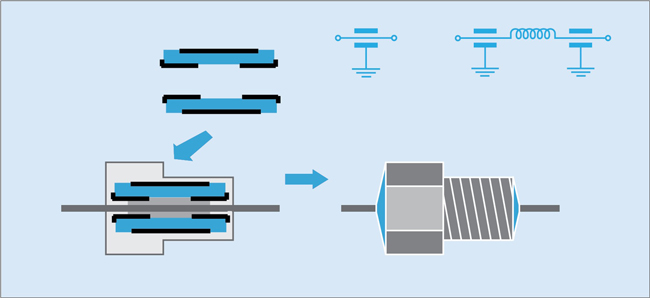
Figure 5 Representative tubular capacitors construction and electrical configurations.
As multilayer ceramic capacitor (MLCC) capabilities have developed, the discoidal capacitor is becoming a popular choice for filters. A diagram of a discoidal capacitor is shown in Figure 6. Using MLCC construction provides a very low inductance, low equivalent series inductance (ESL)/low equivalent series resistance (ESR) capacitor with improved performance and higher capacitance and voltage ranges. With a discoidal capacitor, the electrodes align with the Faraday cage and act as an extension of the cage, improving performance at higher frequencies. MLCCs are also physically much more robust than tubes.
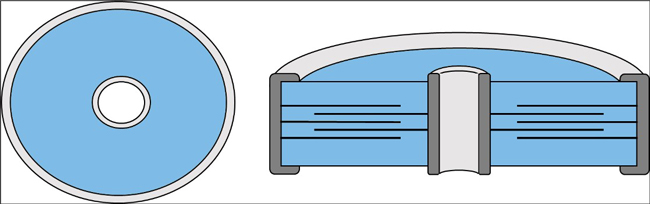
Figure 6 A representation of discoidal capacitor construction.
Planar arrays are the final option this article will consider for EMI filter capacitor construction. A representative diagram for a planar array capacitor is shown in Figure 7. Planar arrays provide capacitance between the outside perimeter and the internal through holes. Because of this construction, a planar array functions much like many discoidal capacitors in one piece of ceramic. This design saves space and weight, allowing for EMI filtering of multiple lines in a compact and efficient design. As a result, planar arrays are the main filter connectors used in high-end military and aerospace equipment.
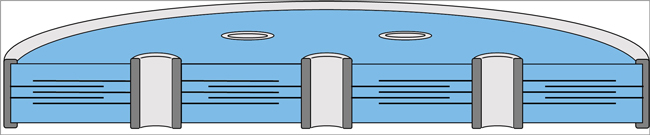
Figure 7 A representation of planar array capacitor construction.
Capacitor Mounting
The ceramic capacitor, which is the heart of the filter, can be damaged by thermal and mechanical shock as well as by overvoltage. Care must be taken to minimize the risk of stress when mounting the filter to a panel and when soldering wire to the filter terminations. The method of mounting the capacitors in the body is also very important because as frequency increases, the wavelength gets smaller. At higher frequencies, any gaps caused by assembly issues, such as missing solder, may allow the signals to get through the panel and this will impact performance.
Thread or Head Size and Shape
Filter heads can be round or hex-shaped. If close mounting pitch is important, a round body style offers the best solution. Round heads are mounted using modified screwdriver blades, which removes the need to allow space for mounting sockets. This allows components to be mounted so that they almost touch each other. This advantage is shown in Figure 8 with representative layouts for round heads versus traditional hexagon heads. Also, note that very small threads are harder to work with and often offer little or no advantage over larger thread sizes.
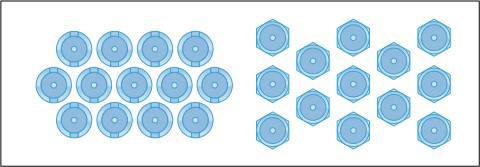
Figure 8 Pitch improvement with round head filters compared to traditional hexagon heads.
SURFACE MOUNT FILTERS
The surface mount filter is the final type to be reviewed in this article. Surface mount filters are a lower-cost alternative to panel mount filters and they offer the highest capacitance and voltage of any filter type. If a filter simply needs to suppress a certain frequency range and does not require the performance a panel mount option provides, a surface mount filter is a much cheaper alternative. However, the tradeoff is lower performance. Another potential drawback of a surface mount filter is that these filters do not sit in a Faraday cage, therefore they only block conducted interference, not radiated interference. There are three distinct families of surface mount filters: C filters, surface mount Pi/C filters and X2Y filters.
C Filters, which are also known as three-terminal chips, use conventional MLCC manufacturing techniques to form a filter that is a short circuit end-to-end and has a capacitance between the end terminals and the side (ground) terminals. The signal is carried through the internal electrodes and the current-carrying capacity is defined by the cross section and number of electrodes in the filter. This is linked to the capacitance of the filter. Compared to conventional two-terminal MLCC devices, the internal inductance between the line and ground is reduced, improving the attenuation performance.
Surface mount Pi filters incorporate two capacitors and an inductor to make a multi-element filter. This results in a sharper cut-off and better low-frequency performance than straight C filters. Current-carrying capacity is defined by the characteristics of the conductor and is independent of the capacitance of the filter.
X2Y filters are manufactured the same way as conventional MLCCs but they have a special internal architecture that results in low ESL through opposing current flows in adjacent parallel plates. These are not feedthrough devices but act as bypass filters, which means these filters are not current-limited. The only signal passing through the chip is the filtered noise to ground. X2Y filters are ideal for twin-line applications such as motors, amplifier inputs or twisted pair, balanced line applications where the filters are fitted between the lines with the center terminal taken to ground. Incorporating the capacitors in a single ceramic element eliminates any capacitance shift through temperature variation.
THE EFFECTS OF THE MOUNTING METHOD ON INSERTION LOSS
When using surface mount filters, it is important to recognize that the board material, thickness and layout, plating finish, grounding efficiency and circuit impedances will all impact the actual performance of the filter in operation. The effect of the board makes it difficult to directly compare parts unless the mounting details are defined. Therefore, it is important to test filters in a circuit to determine the performance level achieved.
CONCLUSION: INCLUDE AN EMI FILTER IN YOUR CIRCUIT DESIGN FROM THE START
EMI filters are often not included during initial design, but when equipment fails an emissions or susceptibility test, it becomes clear that the need to filter the EMI is necessary. Instead of waiting to fail a test or have a field failure, it is best to include an EMI filter in your initial circuit design. As demonstrated throughout this article, any application that needs high reliability is best suited for a panel mount filter. To save space and improve performance, an EMI discoidal style filter is generally the best panel mount option.
An application that can tolerate some noise, like a Wi-Fi router, could use a surface mount filter. This option is cheaper, faster and easier to place on a board and this type of filter saves board space compared to a combination of discrete filter elements. This solution will not approach the performance of a planar filter because the surface mount filter is not sitting in a Faraday cage.