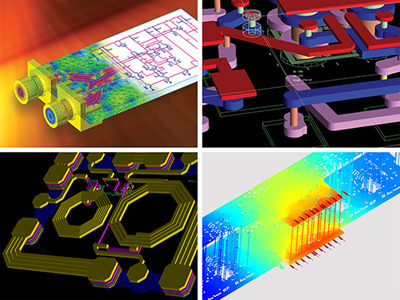
Design Platforms Maximize Performance and Reduce Time-to-Market
Invited Paper with contributions from: Altair, ANSYS, Dassault Systemes - SIMULIA CST, Keysight Technologies and NI AWR Group
Microwave Journal asked some of the leading EDA software companies to describe their respective holistic approaches that help design engineers optimize across multiple tools, to accomplish high performance, reliable designs quickly and efficiently. Here are some comprehensive platforms that can accomplish multiple design tasks in one interface or environment to rapidly get your designs to market.
Altair FEKO, Part of HyperWorks Platform, Altair, Troy, Mich.
Altair’s vision is to transform design and decision making by applying simulation, machine learning and optimization throughout product lifecycles. This is achieved by a combination of simulation software within the HyperWorks platform of innovation, complemented by software related services and consultancy offerings. Engineers are able to accelerate next-generation mobility solutions to meet the challenges of e-mobility development. From smart control design to powertrain electrification and vehicle architecture studies, these solutions enable optimization throughout the development cycle.
Altair FEKO, a computational electromagnetic (EM) software aimed at telecommunications, automobile, aerospace and defense industries, is an integral part of HyperWorks suite. FEKO offers several frequency and time domain EM solvers under a single license. Hybridization of these methods enables the efficient analysis of a broad spectrum of EM problems, including antennas, microstrip circuits, RF components and biomedical systems, the placement of antennas on electrically large structures, the calculation of scattering and the investigation of electromagnetic compatibility (EMC). FEKO also offers tools that are tailored to solve more challenging EM interactions, including dedicated solvers for characteristic mode analysis and bi-directional cable coupling. Special formulations are also included for efficient simulation of integrated windscreen antennas and antenna arrays. Combined with the multilevel fast multipole method and the true hybridization of the solvers, FEKO is considered a market leader for antenna placement analysis.
One of the most notable features of the recent 2018 release is the inclusion of WinProp with FEKO as part of the standard HyperWorks installation. WinProp is a dedicated tool for wave propagation modeling and radio network planning interfacing with FEKO. WinProp’s accurate and fast empirical and deterministic propagation models are available for a wide range of scenarios: rural, urban, indoor, tunnel, vehicular (see Figure 1). WinProp supports arbitrary transmitters including cellular and broadcasting sites, satellites, repeaters and leaky feeder cables. WinProp’s propagation engines include empirical and semi-empirical models (calibration with measurements possible), 3D ray tracing models, as well as the unique dominant path model. Besides the prediction of the path loss, the delay and angular spread can be computed, as well as LOS/NLOS, directional channel impulse response, angular profile and propagation paths (see Figure 2).
Figure 1 Path loss prediction in hybrid urban/indoor scenario.
Figure 2 Full polarimetric analysis.
A few key differentiators of FEKO include:
- A broad and deep technology offering: pre- and post-processing, different solver technologies, multiphysics coupling, strong focus on optimization technology, HPC integrations.
- Units-based subscription licensing model: all the Altair software tools including many third-party products in the Altair Partner Alliance, available under a uniform licensing scheme.
- Unique blend of software and services: complementing the software offering through consultancy that also helps Altair to understand customer needs for future software development.
Figure 3 Adaptive Cruise Control (ACC) Radar System in a Bumper with Paint Layer.
Some of the highlights in the FEKO 2018 release features:
- Characterized surfaces for the ray launching geometrical optics (RL-GO) solver greatly speeds up RL-GO analysis of complex multilayer structures (see Figure 3).
- Cable modeling extensions, including defining a reference direction for a cable path, providing precise control over cable orientation, instead of letting the solver search for the closest ground to the cable path.
- Numerous meshing improvements, including automatic meshing, which now yield different meshes for models, where the mesh size is governed by the geometry curvature rather than EM properties like frequency.
- Support for characteristic mode analysis without mode tracking across frequency.
EM applications vary in complexity and electrical size, and no single numerical method can handle the entire range efficiently. By offering a selection of different solvers, FEKO users can choose the methods most suitable to the problems they are trying to solve, or use more than one solver for cross validation purposes. All solvers are included in FEKO as one package.
ANSYS Electronics Desktop Platform, ANSYS, Canonsburg, Pa.
The ANSYS Electronics Desktop is a design platform created for the electrical engineer. It is a single interface for engineers to access the ANSYS physics solvers (HFSS, HFSS SBR+, Maxwell, Icepak, Q3D Extractor, SIwave) and circuit/system simulators (Nexxim, Simplorer, EMIT) with direct import of ECAD/MCAD geometry. In addition, the desktop includes direct links to the full ANSYS portfolio of thermal and mechanical solvers for comprehensive multiphysics analysis. With ANSYS Electronics Desktop, designers can integrate rigorous EM, thermal and mechanical analysis with system and circuit simulation in a comprehensive, easy-to-use design platform.
ANSYS HFSS is built in the ANSYS Electronics Desktop. The traditional MCAD interface is used by engineers to create 3D models, such as antennas, connectors, enclosures, lead frame IC packages and waveguides. The ECAD interface is for layered design as found in PCBs, IC packages and RF laminates. A unique feature is the desktop’s ability to mix MCAD with ECAD to create assemblies for wireless and electronic products with full 3D HFSS simulation accuracy. HFSS solvers, including the classic finite elements, integral equation, physical optics and shooting and bouncing rays (SBR), can be intermixed as multi-domain (hybrid) solutions to simulate from the electrically small to large in a single project (see Figure 4).
Figure 4 ANSYS Electronics Desktop is a powerful platform with the capability to combine multiple physics, circuits and systems into a single simulation such as the radar system depicted.
The Electronics Desktop’s Solver on Demand technology enables engineers to combine EM simulators with circuit- and system-level simulations to explore complete system performance. Users can insert high frequency and signal integrity analyses into projects that co-exist, with drag-and-drop dynamic links between EM and circuit simulations, for simple problem setup and reliable performance. Working within a single interface, rather than moving back and forth between several different programs, eliminates the need to export data from one program to another. For example, users can insert VRMs, S-parameter elements or IBIS-AMI models into a circuit simulation very easily (see Figure 5).
Figure 5 ANSYS Electronics Desktop integrates ANSYS HFSS calculated loss data with ANSYS Icepak to produce a temperature profile of a ring hybrid coupler.
In addition to its multi-domain and multi-technology design capability, the ANSYS Electronics Desktop includes capabilities such as 3D component library models with encryption, assembly modeling and radio frequency interference (RFI) systems modeling. As communication systems push the limits of component size, weight and performance, engineers must adopt new technologies and smarter workflows. The resulting component engineering and associated intellectual property become increasingly valuable to the component developer and end-user. The ability to share accurate 3D design data among engineering groups while protecting this IP is critical to developing next-generation complexity in a practical manner. The patented 3D EM component technology is a breakthrough in model sharing, allowing engineers to create encrypted, password-protected user models that provide all the information to successfully design RF and microwave systems.
Predicting RFI in complex environments has become an essential part of the design process. The ANSYS Electronics Desktop integrates ANSYS EMIT for modeling installed antenna-to-antenna coupling. The result is a complete solution to reliably predict the effects of RFI in multi-antenna environments with multiple transmitters and receivers. EMIT’s powerful analysis engine computes all important RF interactions including nonlinear system component effects. These effects can produce high order intermodulation products that often lead to RFI. Diagnosing RFI in complex environments is notoriously difficult to perform in a testing environment, but with EMIT, the identification of the root-cause of any interference is rapidly accomplished via graphical signal trace-back and diagnostic summaries that show the exact origin and path that interfering signals take to each receiver (see Figure 6).
Figure 6 ANSYS Electronics Desktop platform can predict RF interference and simulate radio de-sense in electronic devices.
The ANSYS Electronics Desktop fully integrates world-class physics solvers with circuit and system solvers, patented encrypted 3D component libraries for data sharing and RFI prediction capability into a common platform. Using this design platform, RF/microwave designers will be successful addressing the next level of wireless product complexity and system integration.
CST STUDIO SUITE Complete Multi-Domain and Multiphysics Solution
Dassault Systèmes, SIMULIA CST, Darmstadt, Germany
SIMULIA’s CST STUDIO SUITE is a 3D design environment that enables access to EM and multiphysics simulation. Fully parametric models can be constructed in CST STUDIO SUITE or imported through the interface with leading CAD and EDA design tools. Entire EM systems can be designed from their constituent components using the CST System Assembly and Modeling (SAM) framework. Parameter sweeps allow different design configurations to be analyzed in a single simulation flow, while the built-in automatic optimizers can be used to tune and improve the performance of devices.
With Filter Designer 3D, CST STUDIO SUITE features a dedicated design flow, allowing even extremely complex filters to be tuned, with multiple passbands and transmission zeroes, if required. CST’s fast resonant solver and innovative moving mesh method offer smooth convergence, allowing even very sensitive filters to be optimized efficiently. These approaches can save both time and money compared to traditional physical testing, by reducing the number of prototypes required to achieve a design that meets the requirements.
Multiphysics simulation can be important for high-power devices, where excess heat due to EM losses in materials can cause damage and expansion and deformation that detune sensitive components such as filters and resonators. To allow these effects to be simulated and mitigated from the earliest stages of the design process, CST STUDIO SUITE offers integrated thermal and structural mechanical solvers capable of simulating temperature distribution, heat flow, cooling, biological heat effects and thermal expansion.
Once the individual components have been designed, the work of the system integrator begins. For a complex product such as a car, multiple components can be imported from different tools—the car body from one source, the cable harness network from another, the circuit boards from yet another and the communication and radar antennas from the CST antenna tool Antenna Magus—and assembled into a simulation project using SAM.
Antennas and other parts need to be placed in the system in such a way that they work as intended, in what is often a challenging and crowded environment. The metal body of a car or aircraft will affect the radiation pattern of antennas placed on its surface, while the human body can absorb or reflect energy from handheld and wearable devices. CST STUDIO SUITE includes several methods suited to simulating antennas on electrically large platforms, which can be used to calculate the performance of individual antennas and the coupling between multiple antennas (see Figure 7).
Figure 7 Simulated electric fields of an antenna placed on a bus in the CST STUDIO SUITE interface.
EMC and EM interference (EMI) are significant concerns in product design. If not caught as early as possible, installed performance and interference problems can significantly delay the development of a product or require costly and reputational damaging recalls. With the new CST Interference Task, potential interference problems can be identified at the design stage, helping ensure compliance with legal regulations and reducing the risk of unexpected issues emerging during testing.
For devices used near the body, there are also legally-mandated limits on the exposure to RF fields, measured as specific absorption rate (SAR). These, too, can be simulated with CST STUDIO SUITE to check design compliance with regulations.
By integrating all these features into one user interface, CST STUDIO SUITE helps engineers optimize their designs quickly and efficiently and avoid problems that can add to the development time and cost of a project. With CST STUDIO SUITE 2018, CST, now part of the SIMULIA brand of Dassault Systèmes, is integrating its software with the 3DEXPERIENCE platform, which connects CAD, PLM, collaboration and other leading edge simulation software, to provide a complete multi-domain and multiphysics solution.
Keysight PathWave Design--More Creativity, Less Busywork
Keysight Technologies, Santa Rosa, Calif.
Board designs are becoming increasingly complex, with increased substrate layer counts, smaller form factors and limited design space. Additionally, once a design is complete, the designers still need to handle all the logistics, handoffs and liability, making it difficult to spend enough time actually designing and creating new products. To avoid frustration and spend more time innovating, engineers need a way to streamline their workflows.
Keysight’s design platform enables designers to focus on their favorite part of the job: the creative design process. Keysight PathWave Design is a new design environment that gives engineers the space for creativity, data displays for validation and common data formats to share ideas with colleagues. It provides integrated system, circuit and EM simulators, plus optimizers and layout capabilities that seamlessly integrate to save time and frustration in investigating various aspects of the design (see Figure 8).
Figure 8 Keysight PathWave Design offers a variety of libraries, simulators, optimizers, layout views and data displays so design engineers can focus on creating and designing.
Keysight PathWave Design is built on Keysight Advanced Design System (ADS) and other software offered by Keysight EEsof EDA, including EMPro for EM analysis, SIPro for signal integrity analysis and PIPro for power integrity analysis. A benefit of designing with Keysight is the measurement expertise, depth of understanding the standard specifications and breadth of component libraries. The industry-compliant wireless libraries enable verifications of designs to all the latest wireless standards: 5G, LTE-A, 802.11ac, PCI Express, USB 3—and whatever standards the future brings will be added.
A design engineer’s work is not done once the design is complete. The handoff to the design verification test team is not just a simple handshake. Years ago, designs were less complex and specifications less stringent and a simple linear product development lifecycle pipeline worked. But today, the product development lifecycle has been transformed into a matrix of complex relationships between the design, verification and test teams. This is where the power of the Keysight PathWave Platform shines: it not only contains a design environment, but a test environment with common data formats, a consistent user experience and similar control interfaces. It is this integration that bridges the design and test engineers’ worlds, allowing them to speak the same language and interact in a completely new way (see Figure 9).
Figure 9 PathWave Design and PathWave Test eliminate silos between design, verification and test teams, allowing engineers to share data between multiple software programs as shown here for 5G NR signals.
PathWave Test is a test automation environment that optimizes test plans and operates with third-party hardware to provide seamless data transfer and analytics to the design environment and to the manufacturing teams. This makes it much easier for the test teams to go back to the design engineers and let them know of possible problems. This reduces time spent and eases communication in design iterations and troubleshooting, for both design and test engineers.
Both the PathWave Design environment and PathWave Test environment live inside the PathWave Platform, a systems engineering platform that eliminates silos between design, test and manufacturing teams, providing data and immediate insights to accelerate the product development lifecycle. In the future, PathWave will be what a student thinks of when visualizing a design becoming reality.
NI AWR Group, El Segundo, Calif.
The NI AWR Design Environment platform was conceived and developed with RF designers in mind, empowering the individual engineer and engineering teams to address all phases of the design process (exploration, simulation, optimization and verification) prior to manufacturing, while also providing a smooth transition to fabrication and test, with minimal design rework.
Microwave Office circuit design software was introduced 20 years ago at IMS1998 in Baltimore, with a Windows-based user interface and a real-time tuning bar (see Figure 10) that caught the attention of many attendees, putting AWR and its product on the map. From its inception, the overall framework of the software was architected to readily support third-party tools and technologies, to supplement product functionality and offer designers power of choice, as well as maximum flexibility and productivity.
Figure 10 Parametric tuning introduced in Microwave Office software in 1998 has evolved to support large-scale tuning of complex structures.
The NI AWR software platform has expanded to offer more innovations such as AXIEM and Analyst™ native EM solvers, Visual System Simulator™ system simulation software and AntSyn™ antenna synthesis technology, as well as wizard-based features and third-party add-ons that further enhance RF designers’ productivity.
The NI AWR Design Environment user interface is a Windows-based, PC-only platform that has always leveraged application programming interfaces (API) and object-oriented programming with a unique underlying unified data model architecture that links electrical and physical design in a revolutionary way. A change to one is instantly a change to the other and vice-versa, eliminating the manual manipulation required with alternative tools.
Figure 11 Network synthesis addresses multi-band matching challenges.
The environment’s framework is further constructed as a socket for ready plug-and-play of tools and technologies that can be native or from third-party partners. For instance, the EM Socket™ interface within the NI AWR Design Environment platform integrates AXIEM 3D planar and Analyst 3D EM solvers, as well as those from other EM vendors such as Sonnet, SIMULIA CST and ANSYS. Numerous other wizards and add-on modules, whether developed in house or by partner firms, will “socket” into the NI AWR software framework to further enhance engineering productivity.
The high frequency circuit, system and EM capabilities of NI AWR Design Environment software address the key design steps of RF/microwave product development, from characterization and simulation to exploration, optimization, compliance and verification, always mindful of the software team’s mantra to “accelerate customer design success.”
One of the next fronts of innovation for the platform is accelerating design starts and exploration via synthesis technologies and techniques. A new network synthesis capability for creating optimized two-port matching networks with discrete and distributed components, based on user-defined performance goals, is being introduced this year (see Figure 11). The proprietary synthesis algorithm searches for the best circuit typologies and optimizes the component parameter values. This feature joins existing synthesis tools within the NI AWR portfolio that include products such as iFilter™ filter synthesis and AntSyn automated antenna design, synthesis and optimization.
The new-to-market synthesis tool will assist RF design engineers in developing new products directly from performance specifications, greatly accelerating the earliest phases of the design process. The first release of this new module, available as an add-on to the V14 release, will be particularly helpful for challenging broadband single- and multi-stage amplifiers and antenna/amplifier matching networks.